 |
Q1. すべり軸受の欠点はなんですか?
Q2. 軸受メタルの合金はなぜ鉛がつかわれるのか?
Q3. 軸受の摩擦損失を見積もる方法はないか?
Q4. クランクピンの軸受荷重や摺動速度はどのようにもとめるのか?
Q5. 転がり軸受とすべり軸受の摩擦係数はどの程度違うのか。
Q6. 玉軸受の玉の表面粗さはどの程度なのか。
Q7. 軸受をしまりばめで取付ける方法とは。
Q8. 軸受の焼付き損傷(変色、変形、溶着)が発生した。どのような対策をとれば良いのか。
Q9. 軸受異常の有無を判別するのにどのような方法があるのか。
Q10.段付歯車のようにホブ切りできない歯車はどのように歯切りすればよいのか
Q11.かみあい伝達誤差どのように計算されるのか
Q12.浸炭焼入れ法が歯車の強度向上のために用いられるがその理由は。
Q13.諸元設計時モジュール、圧力角は任意に設定してよいのか
Q14.転位係数は小歯車と大歯車にどのように振り分ければよいのか
Q15.接触子にローラを使うときの跳ね返りは何をか?
Q16.切り下げを避けるにはどうすればよいのか?
Q17.そのときの跳ね返りは?
Q18.自由度があらわすものは何ですか?
Q19.リンクを設計する時に他のどんな要素が必要なの?
Q20.低温環境下ではオイルシールを取付けにくい。
Q21.軸の材料と硬さはどのようなものを選べば良いのか。
Q22.オイルシールを取付けた運転初期に回転トルクが大きくなることがある。
Q23.オイルシールのリップから漏れが発生したが、シールに異常は無い。不具合要因は何か。
Q24.リップからの漏れが発生し、リップが軟化していた。不具合要因は何か。
Q25.JIS B 1083「ねじの締付通則」、JIS B 1084「ねじ部品の締付試験方法」の適用範囲について
Q26.ねじの表面処理方法の特徴について
Q27.ねじ部品に使用される材料について
Q28.ボルト疲れ強さに及ぼす加工法の影響について
Q29.ボルトの遅れ破壊について
Q30.たわみ軸継手を使えば軸心出しは必要ないですか。
Q31.大きな軸心のずれがある状態で軸を結合することは何故避けなければらならいのですか。
Q32.運転条件をもとに軸継手を選定する場合、伝達トルクの計算で考慮すべきことは何ですか。
Q33.合成潤滑剤の開発が進んでしますが、考慮すべき点は何ですか。
Q34.潤滑油の選定で重要な性状は何ですか。
Q35.潤滑油のメンテナンスで重要な性状は何ですか。
Q36.固体潤滑剤を被膜として用いる時、膜厚さは厚いほど高寿命となりますか。
Q37.潤滑油の供給過多は副作用となることはありますか。
Q38.セラミックスをしゅう動材に使う場合、最も留意すべき点はどのような点ですか。
Q39.機械的衝撃、熱的衝撃に比較的強いセラミクッスはどのようなものがありますか。
Q40.高分子材料をしゅう動材に使う場合、最も留意すべき点はどのような点ですか。
Q41.コーティング膜は厚いほど寿命が長いと考えよいのですか。
Q42.表面処理を行う場合は処理面は片面だけでよいのですか、両面すべきですか。
Q43.トライボロジー(tribology)とは?
Q44.摩耗の種類について
Q45.潤滑剤について
Q46.流体潤滑について
Q47.真実接触面積について
Q48.トライボロジー(tribology)とは?
Q49.摩耗の種類について
Q50.潤滑剤について
Q51.流体潤滑について
Q52.真実接触面積について
Q53.変速機で、エンジン回転速度を制御できるのはなぜ。
Q54.トルクコンバータのロックアップ領域を拡大すると燃費が向上するのはなぜ。
Q55.変速比はどのように制御しているのか
Q56.入力トルクが小さいところでは、面圧が低くなり、トラクション係数が低くなり、滑らないのか
Q57.トロイダルCVTのバリエータ部の効率は最大どの程度までできるか
Q58.ピストンリングの合い口はなぜ有るのか?
Q59.シール性向上のためには、ピストンリングの本数を多くすれば良いと思われるが?
Q60.漏れガス量が多くなると、どんな悪い事が起こるのか?
Q61.潤滑油の漏れ量が多くなると、どんな悪い事が起こるのか?
Q62.エンジンにおけるピストンリング付近の温度環境はどれ位苛酷なのか?
Q1
すべり軸受の欠点はなんですか?
A1
転がり軸受に比較して、
・機器の起動停止が頻繁におこなわれる場合、停止時には流体潤滑膜の形成が期待できないため、摩耗が大きくなったり、そのときの摩擦力が大きくなったりする点。
・軸受への油の供給が不可欠であり、そのための機構が必要である点。
・軸受け周りの精度が要求される点
などがあげられる。

Q2
軸受メタルの合金はなぜ鉛がつかわれるのか?
A2
合金層の重要な役割としてなじみ性がある。鉛は、柔らかくて融点が低く、油との親和性がよく、金属なので熱伝導性もある程度良好である。これらの特徴から、直接接触が発生した場合の摩擦発熱、温度上昇を抑制でき、容易に変形、摩耗する特徴があり、なじみ性を確保する上で良好な特徴をもつ。そのため、耐疲労性を得るための他の材料と組み合わせて多用されている。

Q3
軸受の摩擦損失を見積もる方法はないか?
A3
流体摩擦は、流体のせん断力を計算することで得られるが、そのせん断力は油膜厚さの逆数に比例し、実際の粘度はせん断速度や圧力、温度にも依存する。実際の油膜厚さの表面粗さレベルの影響が大きいことが考えられる。さらに、境界接触も荷重分担では割合が小さいが摩擦損失に対しては無視できないことも考えられる。よって、軸受の摩擦を精度よく計算する方法はまだ確立されているとはいいがたい。
しかし、演習で示した近似で簡易的に見積もるには、以下の式を用いることで摩擦トルクTfを求めることができる。(記号は演習と同じ)
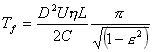

Q4
クランクピンの軸受荷重や摺動速度はどのようにもとめるのか?
A4
ピストン-コンロッド-クランクは、4リンク機構のうちのスライダリンク機構の一例であり、その運動状態はその幾何関係からもとまる。詳細は、このコースのレッスン:リンクなどを参照方。得られた加速度などを用いて、コンロッド、ピストンの重量特性から求めることができる。また、燃焼ガス圧力は、ピストン面積で荷重に変換して、リンク上を伝達されるとして、計算することができる。
摺動速度も、リンク機構の計算結果から、軸-軸受間の相対速度として求める。

Q5
転がり軸受とすべり軸受の摩擦係数はどの程度違うのか。
A5
滑り軸受の摩擦係数は、一般にμ=0.1〜0.01程度であるのに対して、転がり軸受は通常の安定した運転条件で深溝玉軸受を例にとるとμ=0.001程度(面接触→点接触となる)と摩擦係数が1桁以上低くなる。

Q6
玉軸受の玉の表面粗さはどの程度なのか。
A6
玉の表面粗さはJIS B 1501で規定されており、各等級による表面粗さRa(最大)は
G3(3等級) =Ra0.012μm
G5(5等級) =Ra0.02μm
G10(10等級)=Ra0.025μm
となっている。

Q7
軸受をしまりばめで取付ける方法とは。
A7
しめしろの少ない小形の軸受には圧入法を適用する。軸受に均一な力がかかるように当て金を用いて静かに圧入する。油圧ポンプによるプレスの利用が一般的でボルトとナットを利用する方法もある。
しめしろの多い軸受や大形軸受には焼ばめ法を適用する。油の中で軸受を加熱膨張させて軸に取付けるため軸受に無理な力がかからず、短時間で作業がおこなえる(120℃以上で加熱すると軸受の硬さが低下するので、100℃以下で加熱する)。

Q8
軸受の焼付き損傷(変色、変形、溶着)が発生した。どのような対策をとれば良いのか。
A8
焼付き損傷は、軸受内部すきまの過小,潤滑剤の不適または不足,過大荷重等が主な原因である。対策として適正な軸受内部すきまの選定,潤滑方法や潤滑剤の見直し,軸受形式の見直し,軸受損傷の早期発見をおこなう必要がある。

Q9
軸受異常の有無を判別するのにどのような方法があるのか。
A9
音を聞いて判別する方法:音はハウジングに補聴器または聴音棒を当てると良く聞こえる。
運転中の温度で判別する方法:異常現象が起こると温度が高くなるばかりでなく不規則になる。音響検査との併用が有効である。
潤滑剤の状態で判別する方法:潤滑剤のサンプルを採取して汚損や異物、金属粉の混入状態等によって判別する。
振動を測定して判別する方法:定期的に振動を測定することによって軸受の異常を判別する。

Q10
段付歯車のようにホブ切りできない歯車はどのように歯切りすればよいのか
A10
段付歯車をホブで加工しようとするとホブが隣の歯車に干渉してしまう場合がある。このような場合にはピニオンカッタを用いる。
ピニオンカッタ切りとは、歯車の形状をしたピニオンカッタに歯車の歯すじ方向の往復運動を与え,その現わす仮想歯車に歯車材を正しくかみあわせて、創成歯切りする方法である。内歯車の歯切りにも用いられる。

Q11
かみあい伝達誤差どのように計算されるのか
A11
かみあい伝達誤差とは、入力歯車の回転に対する出力歯車の回転遅れ変動(回転ムラ)のことである。この回転ムラは、かみあいの進行に伴う同時かみあい歯数の変化による歯対のばね剛さの変動や歯面誤差の変動から歯車1回転中に歯数回生じる周期関数となっている。また、負荷の影響も大きく受ける。
この計算方法としては、久保,梅澤の方法(機論43巻371号 p2771)が広く用いられている。

Q12
浸炭焼入れ法が歯車の強度向上のために用いられるがその理由は。
A12
低炭素鋼あるいは合金鋼を浸炭雰囲気の中で変態点以上の温度に保持すれば、表面より炭素が浸入して内部に拡散していく。浸入炭素量は表面がもっとも多く内部に進むにしたがって漸減するから、これを焼き入れると表面は硬化するが内部は硬化しない。これにより、表面は硬くて耐磨耗性があり、内部は靭性に富むという高強度の性質が与えられる。

Q13
諸元設計時モジュール、圧力角は任意に設定してよいのか
A13
JISには標準のモジュール,圧力角が設定されていますが、ノイズ,強度および生産性のバランスの取れた最適の歯車諸元とするためには、基本的には最適なものを選定する。ただし、この場合、その歯車に対して専用の工具(ホブ,シェービングカッタあるいは砥石)を準備する必要がある。自動車用歯車のように大量に生産される歯車に対しては任意のモジュール,圧力角の設定がなされている。
製作数が少なく、ノイズ,強度に対する要求があまり厳しくない場合には既存の標準の工具で製作できる歯車諸元とするのが加工コストおよび納期上望ましい。

Q14
転位係数は小歯車と大歯車にどのように振り分ければよいのか
A14
任意の中心距離を持つ2軸間に任意の歯数比の歯車対を収めるためには転位する必要があり、この時大小歯車の転位係数の和は一定となる。強度面からこの振り分けには2つの考え方がある。一つは、小歯車と大歯車の歯元曲げ応力を同等とする等応力設計で、歯元の危険断面の歯厚が同等となるように転位を振り分ける。もう一つは破損に至る時間を同等とする等寿命設計で、歯数比の大きい歯車対に対して用いられる場合が多い。この場合、S-N線図から歯数比に相当する寿命比から応力比を求め、それを実現するように転位を振り分ける。小歯車の転位係数ををプラス側に大きくする。

Q15
接触子にローラを使うときの跳ね返りは何をか?
A15
ローラを接触子に選定することにより、当然フリクションが低減するといった
メリットが得られるが、跳ね返りとして@コストA重量Bサイズが考えられる。
特に、重量増は高回転が要求される機構には不適である。

Q16
切り下げを避けるにはどうすればよいのか?
A16
切り下げはローラ半径Rrがローラ軌跡の最小曲率半径ρminより小さいときに発生する。
そのため、Rrを小さくするか、ρminを大きくする必要がある。
Rrはローラー径を小さくすることで対応できる。
一方ρminの方はカムのベース径を大きくすることで大きくできる。

Q17
そのときの跳ね返りは?
A17
ローラー径を小さくすると接触面圧が大きくなるし、極端な小型化は不可能である。
カムのベース径は大きくすることで全体のサイズが大きくなり、重量も増す。

Q18
自由度があらわすものは何ですか?
A18
リンクの自由度はそのリンクがどのように動けるかをあらわものです。
自由度0はずべてのリンクがお互いの位置関係を変えることができないわけです。
自由度1はひとつのリンクを動かすことができ、その動きに対して、他のリンクは決まった ある1つの動きを持つということです。
自由度2は利とつのリンクを動かしても、他のリンクが決まった位置をもてない、 つまり、まだ自由に動けることを示します。自由度2であれば、2個のリンクを
決めないと、他のリンクの位置が決まらないことを示しています。

Q19
リンクを設計する時に他のどんな要素が必要なの?
A19
リンクは動くことによりすべてに加速度が働き慣性力が生まれます。
それぞれのリンクに適した強度計算を行なうのは当然ですが、 同時に軸受け部の潤滑までも考慮する必要があります。

Q20
低温環境下ではオイルシールを取付けにくい。
A20
オイルシールを暖めてシールリップの柔軟性を回復させるとスムーズに取付けることができる。

Q21
軸の材料と硬さはどのようなものを選べば良いのか。
A21
軸の材料は機械構造用炭素鋼・低合金鋼・ステンレス鋼を用いる。黄銅・青銅・アルミニウム・亜鉛・マグネシウム合金等の軟らかい材料は、低速・清浄な環境など特定の場合を除いて適さない。硬さは、一般に30HRC以上を選定する。ダスト・汚れ油等の環境で使用する場合にはさらに硬い方が良く、傷つき防止にもなる。

Q22
オイルシールを取付けた運転初期に回転トルクが大きくなることがある。
A22
軸とリップの摩擦係数が安定しない期間中に発生するもので運転時間の経過(1〜2時間)に伴い、なじみによって摩擦係数が安定するため回転トルクも安定する。オイルシールのリップには初期潤滑のために適切で清浄な潤滑油を塗布する。

Q23
オイルシールのリップから漏れが発生したが、シールに異常は無い。不具合要因は何か。
A23
軸径小、軸表面の粗さ不適、軸表面のきず、軸表面の加工リード目、リップの追従性不足、取付け時の異物付着等が主な原因である。対策として軸寸法の適正化、軸表面の粗さの改善、軸のばり、かえりの除去または軸交換、研磨方法の変更、心出し改善、取付け時の取扱い等に注意する必要がある。

Q24
リップからの漏れが発生し、リップが軟化していた。不具合要因は何か。
A24
シールの洗油・有機溶剤への長期浸せき、ゴム材料の不適等が主な原因である。対策としてオイルシールの洗浄は使用する潤滑剤でおこなう、潤滑剤で膨潤しないゴム材料に変更する(6.ゴム材料の種類と特長を参照)等をおこなう必要がある。

Q25
JIS B 1083「ねじの締付通則」、JIS B 1084「ねじ部品の締付試験方法」の適用範囲について
A25
本規格はボルト・ナットの組み合わせを適用範囲としているが、それ以外のねじ部品による締付及びねじ部品と構造体のねじとを組み合わせた締付に対しても準用することができる。ただし、おねじ部品に圧縮力を与える止めねじ類及びおねじ部品自体でねじたてをする木ねじ、タッピンねじ類並びに特別な戻り止め機能を付与したねじ部品の締付に対しては適用できない。

Q26
ねじの表面処理方法の特徴について
A26
代表的表面処理として、電気亜鉛めっき、電気合金めっき、ダクロ皮膜がある。表面処理の目的は防食と装飾が考えられる。電気亜鉛めっきの耐食性は鉄鋼素地上の亜鉛が鉄より電気化学的に卑なため鉄を保護する犠牲防食と亜鉛表面のクロメート皮膜が亜鉛を保護する防食が重なったものである。電気合金めっき(Zn-Fe,Zn-Ni)はZn単体の数倍の耐食性を得ることができる。しかし高強度ボルト(10.9,12.9級)においては電気メッキによる水素脆性の影響を受けやすくなる。一方ダクロ皮膜(亜鉛末クロム酸皮膜)は、電気メッキによらない耐食性皮膜であり水素脆性の危険がないため高強度ボルトに適する。

Q27
ねじ部品に使用される材料について
A27
JISでは、鉄鋼・ステンテス鋼・非鉄(銅・銅合金・アルミニウム合金)を規定しており、主な規格はJIS B 1051「鋼製のボルト・小ねじの機械的性質」、JIS B 1054「ステンレス鋼製耐食ねじ部品の機械的性質」、JIS B 1057「非鉄金属製ねじ部品の機械的性質」である。JIS B 1051「鋼製のボルト・小ねじの機械的性質」は、強度区分3.6〜12.9(最小引張強度330MPa〜1220MPa)までの10段階、JIS B 1054「ステンレス鋼製耐食ねじ部品の機械的性質」は、オーステナイト系は強度区分50,70,80(最小引張強度500,700,800MPa)の3段階、フェライト系は強度区分45,60(最小引張強度450,600MPa)の2段階、マルテンサイト系は強度区分50,70,80(最小引張強度500,700,800MPa)の3段階、JIS B 1057「非鉄金属製ねじ部品の機械的性質」は、銅合金系は材質区分CU1〜CU7(最小引張強度240〜640MPa)の7段階、アルミニウム合金系は材質区分AL1〜AL6(最小引張強度270〜510MPa)の6段階である。

Q28
ボルト疲れ強さに及ぼす加工法の影響について
A28
ボルトの疲れ強さは転造ダイスの種類、転造時間、転造圧力によって影響を受ける。切削加工後調質し谷底のみ転造したものが最も疲れ強さが向上する。しかし、全ねじ山を丸ダイスとか平ダイスで転造する一般的な製造方法の場合には転造後熱処理を行うのが一般的である。そのような場合には疲れ強さは切削したボルトの場合と変わらない。

Q29
ボルトの遅れ破壊について
A29
遅れ破壊は、1.2GPa以上の引張強さを有する摩擦接合用高力ボルトを使用する場合に考慮しなくてはならない問題である。遅れ破壊は常温で静的な引張負荷あるいは曲げ負荷がある時間加わった後、外見上塑性変形を伴わず突然破壊する現象である。機構は(1)水素脆化(2)応力腐食割れの二つに大別される。前者は鋼中に何らかの要因によって浸入した水素が応力集中部近傍に集中しカソード割れを引き起こすことによる。防止は脱水素処理を行うとか電気メッキを避けるなどして行っている。後者はき裂先端がアノードとなり材料が選択的に溶解されていくことによってき裂が進展していくことによって起こる。オーステナイトステンレス鋼が食塩水程度の電解質水溶液中で起こるものが該当する。

Q30
たわみ軸継手を使えば軸心出しは必要ないですか。
A30
たわみ軸継手でも軸心の狂いは必ず許容範囲があります。メーカーカタログ等などで許容値を確認し、心ずれ量がその値以下になるまで心出しすることが必要です。

Q31
大きな軸心のずれがある状態で軸を結合することは何故避けなければらならいのですか。
A31
大きな心ずれは振動の原因になりす。また、その起振力が原因で、軸、軸継手などが破壊することもあり、非常に危険です。

Q32
運転条件をもとに軸継手を選定する場合、伝達トルクの計算で考慮すべきことは何ですか。
A32
まず、伝達動力と軸の回転数をもとに伝達トルクを計算します。次に、負荷、速度、心ずれ量をもとに、補正係数をカタログなどから選び、補正トルクを計算します。この補正トルク以上の許容伝達トルクを持つ軸継手を選びます。

Q33
合成潤滑剤の開発が進んでしますが、考慮すべき点は何ですか。
A33
確かに合成潤滑剤の進歩は著しいですが、一般に鉱油に比べて高価です。期待する性能とコストのバランスをよく考えることが必要です。

Q34
潤滑油の選定で重要な性状は何ですか。
A34
動粘度、全酸価、全塩基価、引火点、流動点などです。特殊な環境で使用する場合は事前に油メーカとよく相談することを薦めます。

Q35
潤滑油のメンテナンスで重要な性状は何ですか。
A35
動粘度、全酸価、全塩基価、不溶解分、水分、夾雑物です。

Q36
固体潤滑剤を被膜として用いる時、膜厚さは厚いほど高寿命となりますか。
A36
そうとは限りません。膜厚さが厚いと剥離を起こしやすくなるものや、多量の摩耗粉の発生ににより、不具合を起こす場合もあります。固体潤滑被膜はその種類ごとにおおよその最適膜厚さが決まっていますので、しゅう動部の設計する前にメーカカタログをよく読むこと、必要に応じてメーカと相談することが重要です。

Q37
潤滑油の供給過多は副作用となることはありますか。
A37
あります。たとえば、高速回転機械の転がり軸受は供給される油の量が多いとその攪拌による熱により高温となり危険です。潤滑油は一般に冷却作用がありますが、潤滑法によっては逆に温度上昇をもたらすこともあり、供給潤滑油量を管理する必要があります。

Q38
セラミックスをしゅう動材に使う場合、最も留意すべき点はどのような点ですか。
A38
セラミックスは金属材料に比べてじん性に劣りますから、得に応力集中、片当たり、衝撃荷重を避ける設計にしなければなりません。

Q39
機械的衝撃、熱的衝撃に比較的強いセラミクッスはどのようなものがありますか。
A39
機械的衝撃にはジルコニア、窒化けい素が、熱的衝撃には窒化けい素、炭化けい素が比較的強いです。

Q40
高分子材料をしゅう動材に使う場合、最も留意すべき点はどのような点ですか。
A40
高分子材料は温度によって強度が大きく変わりますから、先ずは適用温度範囲も調べてください。また、耐荷重能、限界PV値、クリープ特性なども重要です。

Q41
コーティング膜は厚いほど寿命が長いと考えよいのですか。
A41
そうとは限りません。厚すぎると剥離しやすくなる場合もあり、また、多量の摩耗粉が発生し、不具合を発生する場合があります。各コーティング膜にはおおよその最適膜厚さがありますので、メーカのカタログをよく調べるとともに、必要に応じてメーカと相談することを薦めます。

Q42
表面処理を行う場合は処理面は片面だけでよいのですか、両面すべきですか。
A42
表面処理材としゅう動条件によって変わります。すべり摩擦面で軟質被膜を使う場合は、片面のみ処理した方が良い場合がありますが、その場合は相手面の粗さを小さくしておく必要があります。表面処理する目的と材料同士の相性をよく把握する必要があり、メーカおよび専門家とよく相談して決めるべき問題です。

Q43
トライボロジー(tribology)とは?
A43
定義は、「相対運動をして相互に影響しあう二表面、ならびにそれに関連する諸問題と実際についての科学と技術」であり、ギリシャ語のtribos(摩擦する)が語源。初めは「潤滑(lubrication)」という言葉しかなかったが、1966年、イギリス教育科学省の潤滑技術委員会による報告書の中で、潤滑関連の学問技術の範囲に対する社会の認識を改めるため、「トライボロジー」が作られ提案された。日本においては「潤滑」と「トライボロジー」の両方が使われていて、意味するところは同じと解されているが、「潤滑」は摩擦を低下させる
参考文献:
トライボロジー入門 摩擦・摩耗・潤滑の基礎 岡本純三、中山景次、佐藤昌夫共著 幸書房

Q44
摩耗の種類について
A44
代表的な摩耗の種類としては次の4種類が挙げられる。(1)凝着摩耗:凝着部において、表面間に相対運動があると凝着部付近で破断が生じ、相手面に移着する。これが繰返され、移着物が成長し、最後には接触面から摩耗粉として排出されるという摩耗。(2)アブレシブ摩耗:一方の硬い凹凸面が相手面を削ることにより生じる摩耗。ざらつき摩耗、凹凸摩耗、研削剤摩耗などとも呼ばれる。(3)腐食摩耗:雰囲気中に水分、酸などの腐食性物質が存在することにより、固形物質がなくても生じる摩耗。潤滑油中に水が入ったり、油が劣化して酸ができたりしていると発生する。(4)表面疲れ:転がり接触をするニ物体の接触面付近の材料内部では、歪みとせん断応力が発生する。このせん断応力の繰返しにより内部にクラックが発生し、表面がはがれることにより生じる摩耗。摩耗には他にも多くの種類があり、通常はそれらが複合して生じることが多い。
参考文献:
トライボロジー入門 摩擦・摩耗・潤滑の基礎 岡本純三、中山景次、佐藤昌夫共著 幸書房

Q45
潤滑剤について
A45
潤滑剤は液体の潤滑油、半固体状のグリース、固体潤滑剤に大別される。潤滑油の多くは石油系潤滑油であるが、動植物油、合成潤滑油、エマルジョンなどの水性潤滑剤も使用される。グリースは主として基油(ベースオイル)、増ちょう剤及び添加剤からなる。基油としては一般に石油系潤滑油が用いられる。増ちょう剤は基油を半固体または固体状にするためのもので、石けん系、非石けん系に分類できる。固体潤滑剤としては、二硫化モリブデンや黒鉛等の無機化合物、四ふっ化エチレン樹脂等の有機化合物、銀、鉛等の金属、WB−Ag−Ni等の混合物に主に分類される。
参考文献:
トライボロジー 理工学社、山本雄二・兼田禎宏共著

Q46
流体潤滑について
A46
二表面の相対運動を円滑にし、摩擦や摩耗を防ぐには、二面間に流体が存在し、それにより二面間が完全に引き離された状態にあることが重要である。そのためには、二面間の流体に圧力が発生し、それにより荷重が支えられることが重要で、これを流体潤滑という。摩擦係数について言えば、完全な流体潤滑状態にある摩擦面では、その値が0.001
から0.0001 程度であることが多い。このように摩擦係数が、したがってそこで熱に変換されるエネルギが小さいことと、摩擦面を通過する流体による冷却が可能であることのために、似たような条件で比較すれば、摩擦面の温度上昇が一般に小さい。もう一つ重要な点は、二つの固体面の間に流体膜がはさまれているために、摩擦面の損傷がきわめて軽微である。このような利点があるので、流体潤滑は一名完全潤滑とも言われ、摩擦面は一般に、できる限りこの状態に保つのが望ましい。
参考文献1:
「トライボロジー入門 摩擦・摩耗・潤滑の基礎」 著者:岡本純三、中山景次、佐藤昌夫
参考文献2:
「トライボロジー概論」 著者:木村好次、岡部平八郎

Q47
真実接触面積について
A47
工業的に取扱う表面は粗さを持っている。粗さを持った2つの表面を接触させた場合、実際に接触している面積(真実接触面積)は、見かけの面積に比べて極めて小さいことが普通である。真実接触面積の一つひとつは集中接触になっており、わずかな面積に荷重が集中するため、接触部においては完全に塑性変形を生じていると考えられる。実際の機械の摩擦面は繰返し摩擦されることが多く、作動初期には塑性的接触をしていた摩擦面も次第になじみ、定常状態に達した後は、突起間の接触は弾性変形の範囲に留まり、荷重は弾性的に支持されるようになる。
参考文献:
トライボロジー,山本雄二,兼田禎宏,理工学社

Q48
トライボロジー(tribology)とは?
A48
定義は、「相対運動をして相互に影響しあう二表面、ならびにそれに関連する諸問題と実際についての科学と技術」であり、ギリシャ語のtribos(摩擦する)が語源。初めは「潤滑(lubrication)」という言葉しかなかったが、1966年、イギリス教育科学省の潤滑技術委員会による報告書の中で、潤滑関連の学問技術の範囲に対する社会の認識を改めるため、「トライボロジー」が作られ提案された。日本においては「潤滑」と「トライボロジー」の両方が使われていて、意味するところは同じと解されているが、「潤滑」は摩擦を低下させる
参考文献:
トライボロジー入門 摩擦・摩耗・潤滑の基礎 岡本純三、中山景次、佐藤昌夫共著 幸書房

Q49
摩耗の種類について
A49
定義は、「相対運動をして相互に影響しあう二表面、ならびにそれに関連する諸問題と実際についての科学と技術」であり、ギリシャ語のtribos(摩擦する)が語源。初めは「潤滑(lubrication)」という言葉しかなかったが、1966年、イギリス教育科学省の潤滑技術委員会による報告書の中で、潤滑関連の学問技術の範囲に対する社会の認識を改めるため、「トライボロジー」が作られ提案された。日本においては「潤滑」と「トライボロジー」の両方が使われていて、意味するところは同じと解されているが、「潤滑」は摩擦を低下させる技術として狭義に解釈されることもある。
参考文献:
トライボロジー入門 摩擦・摩耗・潤滑の基礎 岡本純三、中山景次、佐藤昌夫共著 幸書房

Q50
潤滑剤について
A50
潤滑剤は液体の潤滑油、半固体状のグリース、固体潤滑剤に大別される。潤滑油の多くは石油系潤滑油であるが、動植物油、合成潤滑油、エマルジョンなどの水性潤滑剤も使用される。グリースは主として基油(ベースオイル)、増ちょう剤及び添加剤からなる。基油としては一般に石油系潤滑油が用いられる。増ちょう剤は基油を半固体または固体状にするためのもので、石けん系、非石けん系に分類できる。固体潤滑剤としては、二硫化モリブデンや黒鉛等の無機化合物、四ふっ化エチレン樹脂等の有機化合物、銀、鉛等の金属、WB−Ag−Ni等の混合物に主に分類される。
参考文献:
トライボロジー 理工学社、山本雄二・兼田禎宏共著

Q51
流体潤滑について
A51
二表面の相対運動を円滑にし、摩擦や摩耗を防ぐには、二面間に流体が存在し、それにより二面間が完全に引き離された状態にあることが重要である。そのためには、二面間の流体に圧力が発生し、それにより荷重が支えられることが重要で、これを流体潤滑という。摩擦係数について言えば、完全な流体潤滑状態にある摩擦面では、その値が0.001
から0.0001 程度であることが多い。このように摩擦係数が、したがってそこで熱に変換されるエネルギが小さいことと、摩擦面を通過する流体による冷却が可能であることのために、似たような条件で比較すれば、摩擦面の温度上昇が一般に小さい。もう一つ重要な点は、二つの固体面の間に流体膜がはさまれているために、摩擦面の損傷がきわめて軽微である。このような利点があるので、流体潤滑は一名完全潤滑とも言われ、摩擦面は一般に、できる限りこの状態に保つのが望ましい。
参考文献1:
「トライボロジー入門 摩擦・摩耗・潤滑の基礎」 著者:岡本純三、中山景次、佐藤昌夫
参考文献2:
「トライボロジー概論」 著者:木村好次、岡部平八郎

Q52
真実接触面積について
A52
工業的に取扱う表面は粗さを持っている。粗さを持った2つの表面を接触させた場合、実際に接触している面積(真実接触面積)は、見かけの面積に比べて極めて小さいことが普通である。真実接触面積の一つひとつは集中接触になっており、わずかな面積に荷重が集中するため、接触部においては完全に塑性変形を生じていると考えられる。実際の機械の摩擦面は繰返し摩擦されることが多く、作動初期には塑性的接触をしていた摩擦面も次第になじみ、定常状態に達した後は、突起間の接触は弾性変形の範囲に留まり、荷重は弾性的に支持されるようになる。
参考文献:
トライボロジー,山本雄二,兼田禎宏,理工学社

Q53
変速機で、エンジン回転速度を制御できるのはなぜ。
A53
タイヤの回転速度は車速に比例する。変速機は、エンジンとタイヤの回転速度の比率を変化させるので、エンジン回転を制御することになる。

Q54
トルクコンバータのロックアップ領域を拡大すると燃費が向上するのはなぜ。
A54
トルクコンバータは、トルク増幅機能のある流体継ぎ手である。主な機能は、発進時などの車両停止状態から、滑りを伴ないながらエンジンの回転力を伝達すること(滑り無しではエンジンが止まってしまう)、および、エンジンのトルク変動を遮断することである。良好な発進性と振動遮断の性能から広く使用されているが、滑りを伴なわずに回転力を伝える事ができず効率が悪い。ロックアップは、クラッチによりトルクコンバータの機能が不要な状態での滑りを防止し、伝達効率を向上する。

Q55
変速比はどのように制御しているのか
A55
パワーローラが正のトルク伝達により入出力ディスクから受ける力と同じ方向へオフセットすると変速比(出力ディスク回転半径/入力ディスク回転半径)が大きくなる方へ、逆にオフセットすると変速比が小さくなる方へ変速する。この特性を用いて、油圧ピストンでオフセットを操作して傾転角度を制御することで変速比の制御を行っている。

Q56
入力トルクが小さいところでは、面圧が低くなり、トラクション係数が低くなり、滑らないのか
A56
ローディングカムと直列に、皿ばねを設けて、推力に予圧を与えて、滑りを防止している。

Q57
トロイダルCVTのバリエータ部の効率は最大どの程度までできるか
A57
パワーローラベアリングなどの改良により、バリエータ部のみの効率は97%程度まで可能になる。

Q58
ピストンリングの合い口はなぜ有るのか?
A58
合い口は、ピストンリング外径とシリンダライナ内径の違いを吸収するためのもので、両者の材質(熱膨張係数)、温度、などの違いで生じる熱膨張差に起因するものです。合い口寸法は、生産時のバラツキや吸収すべき熱膨張量などを勘案して、最小の値に設定されます。

Q59
シール性向上のためには、ピストンリングの本数を多くすれば良いと思われるが?
A59
ラビリンス構造を強固にするためには、ピストンリング本数の増加は勿論有効です。しかし同時に、摩擦損失が増大するだけでなく、ピストンリングを格納するピストンサイズ大型化に伴うエンジンサイズの大型化、など、その跳ね返りは極めて大きくなります。

Q60
漏れガス量が多くなると、どんな悪い事が起こるのか?
A60
コンプレッサーやエンジンなどにおいて漏れガス量が多いという事は、せっかく仕事をしようとしている作動ガスが減る訳なので、ポンプとしての効率が悪化します。またエンジンの場合には、漏れガスの成分として燃料の未燃分も含まれており、これが潤滑油に溶け込むと潤滑油の劣化を早めてしまう恐れがあります。

Q61
潤滑油の漏れ量が多くなると、どんな悪い事が起こるのか?
A61
コンプレッサーにおいて潤滑油が多く漏れてしまうと、作動ガス(空気)に潤滑油が混ざってしまうので、圧縮ガスとしての清浄性が劣化してしまいます。またエンジンにおいて潤滑油が漏れ燃焼室に上がってしまうと、その潤滑油が直接燃えてしまうので、排気ガスとしての清浄性が劣化してしまいます。さらにどんな機関においても、潤滑油を再給油するインターバルが短くなり、メインテナンスの頻度とコストが高くなってしまいます。

Q62
エンジンにおけるピストンリング付近の温度環境はどれ位苛酷なのか?
A62
概略、燃焼ガスにさらされるピストンは300℃位、冷却水にさらされるシリンダライナは200℃位、その間に存在するピストンリングは、略中間的な250℃位、というイメージです。このような状況においてもエンジンとして問題なく運転できるのは、摺動部の油膜形成と潤滑油の冷却効果によって、良好な潤滑状態が維持できているからです。

|
|
 |