■破壊とは何か■
Q1_1.応力の工学的な意味と、その単位はなんですか?
Q1_2.「間接疲労」とはどのような疲労のことですか?
Q1_3.合計の242件とは、具体的に何をもとにした数字ですか?
Q1_4.応力集中部というのは、どのような部分のことですか?
Q1_5.「Fail Safe Design」の例を教えてください。
Q1_6.強度低下の原因について詳しく教えてください。
■代表的な破壊の種類■
Q2_1.なぜカップ&コーンの形状の破面になるのですか?
Q2_2.「等軸ディンプル」と「伸長形ディンプル」の違いはどうして出てくるのですか?
Q2_3.破面写真のA点とB点に注目したのはなぜですか?
Q2_4.シャルピー吸収エネルギー遷移曲線からどのようなことが分かるのですか?
Q2_5.なぜ「シェブロン・パターン」のような模様ができるのですか?
Q2_6.ぜい性破壊が原因で発生した事故はあるのですか?
Q2_7.疲労破壊の破面が比較的滑らかな面になるのはなぜですか?
Q2_8.なぜ垂直応力に直角な面から45度傾いた面上に起点が存在するのですか?
Q2_9.き裂が伝ぱする部分のひし形のマークは何ですか?
Q2_10.疲労破壊が原因で発生した事故はあるのですか?
Q2_11.結晶内の化学反応について詳しく解説してください。
Q2_12.粒内破壊と粒界破壊はどのように見分けるのですか?
Q2_13.粒界の三重点に応力が集中するのはなぜですか?
■疲労き裂の発生と伝ぱ■
Q3_1.「すべり線よりすべり帯のほうが黒っぽく見える」のはなぜですか??
Q3_2.ストライエーションの形成機構について詳しく教えてください。
Q3_3.疲労限とは何ですか?
Q3_4.△Kの意味について教えてください。
Q3_5.Φには工学的にどのような意味があるのですか?
Q3_6.材料定数の工学的意味と、その関係式について教えてください。
■疲労限と微視的停留き裂■
Q4_1.材料により疲労限の有無があるのはなぜですか?
Q4_2.微視的停留き裂のき裂の先端部の硬さが応力の繰返しによって硬くなるのはなぜですか?
Q4_3.微視的停留き裂が認められない高マンガン鋼でも疲労限が存在するのですか?
■寸法効果■
Q5_1.寸法効果は、いろいろな種類の応力についてもいえることですか?
■破損解析の具体的手法■
Q6_1.破損解析から新技術あるいは新商品が開発された例を教えてください。
Q6_2.PL法による世の中の変化の例を教えてください。
Q6_3.フラクトグラフィとは何ですか?
■身近な破損事例への適用■
Q7_1.0から までの積分が実行できない理由を教えてください。
Q7_2.焼入れ・焼き戻し処理材とはどのような材料ですか?
Q7_3.疲労破面率が大きいと、変動応力を考慮しなくともよいのはなぜですか?
■破壊解析事例1■
Q8_1.メタルフローとき裂の進展の方向が一致するのが一般的なのでしょうか?
Q8_2. なぜ試験片はこのような形状なのですか?
Q8_3.なぜき裂の伝ぱ速度としてストライエーションの間隔を使えるのですか?
Q8_4.スミスの解を用いて換算すると、なぜ△KB=0.5△KAとなるのですか?
Q8_5.初期き裂の深さを0.5mmとし、初期の欠陥のない状態から0.5mmのき裂が生じるまでの繰返し数を全繰返し数の約50%としているのはなぜですか?
Q8_6.このグラフの意味を教えてください。
■破壊解析事例2■
Q9_1.なぜ、アークストライクが破壊の起点と言えるのですか?
Q9_2.SCM440がアークストライクに弱い理由は何ですか?
■破壊解析事例3■
Q10_1.「菊の花状の模様」ができるのはなぜですか?
Q10_2.肉盛り溶接と、その影響について教えてください。
Q10_3.なぜβがβ1とβ2の掛け算になるのですか?
Q10_4.「最大捩り応力は定格トルクの1.5倍程度」なのはなぜですか?
Q10_5.それぞれの対策について詳しく教えてください。
Q10_6.仕上げ精度を上げると、なぜ疲労限が約20%も向上するのですか?
■破壊解析事例4−事例■
Q11_1.なぜ疲労限が60分の1程度に低下してしまったのですか?
Q11_2.なぜこの写真からき裂の方向がわかるのですか?
Q11_3.なぜ疲労破面率が高いと、繰返し応力がボルトの疲労限に近いといえるのですか?
Q11_4.設計では繰返し応力が発生しないはずのボルトがなぜ疲労破壊したのですか?
■破壊解析事例4−まとめ■
Q12_1.ボルトの疲労寿命を長くするには、《材質を軟質材にする》、《オスとメスの締め付けている位置をずらす》とありますが、そうするとなぜ疲労寿命が長くなるのですか?
Q12_2.「応力の流れ」とはどのようなことですか?
Q12_3.それぞれの材質の特徴などを説明してください。
Q12_4.このような形状にすると荷重分布が均一になるのはなぜですか?
■破壊とは何か■
Q1_1
応力の工学的な意味と、その単位はなんですか?
A1_1
応力とは単位面積あたりの力を意味します。したがって、通常、工学単位ではkgf/mm2 、SI単位ではMPa、またはN/mm2を使用しています。たとえば、異なる材料の強さを比べる場合、寸法が異なると公平にならないので、基準を統一して比較するわけです。

Q1_2
「間接疲労」とはどのような疲労のことですか?
A1_2
たとえば、機械のA部品が疲労破損したとします。 A部品の破損に付随して、ほとんど同時にB部品も破損するような場合が現実的に起こり得ます。このB部品は、静的に破損していたと考えます。破損原因を特定する場合、A部品は疲労破損で、B部品は静的破損と分類されます。しかし、B部品は、A部品が破損しなければ、破損に至ってはいないと考えられますので、間接的には疲労破損である、すなわち、間接疲労であると判断できるわけです。
また、間接疲労を疲労の範疇に含めた理由は、破損原因を統計的に分類した場合、静的破損の割合が全体の13%もあり、現実とはマッチしないのではないかと判断したからです。

Q1_3
合計の242件とは、具体的に何をもとにした数字ですか?
A1_3
新日本製鉄及びその関連企業で、1985年〜1995年の10年間に発生した事例をもとにまとめています。

Q1_4
応力集中部というのは、どのような部分のことですか?
A1_4
応力集中は、寸法形状に著しい変化があるところに生じます。すなわち、突起や凹みが存在している部分で、この部分を応力集中部といいます。

Q1_5
「Fail Safe Design」の例を教えてください。
A1_5
もっとも身近な例として、自転車のブレーキや補助バッテリーのついた充電式電気かみそりを挙げることができるでしょう。 前者の場合、通常後輪用ブレーキを使用しますが、万が一これが故障しても、前輪用ブレーキで安全性を確保できます。 また、後者の場合、電気かみそりの使用中電気切れで突然動かなくなる場合があっても、補助バッテリーの方にスイッチを切り替えることができます。一般に、人命に著しい影響を及ぼすような設備には、たいていこのような「Fail Safe Design」の考えが導入されています。

Q1_6
強度低下の原因について詳しく教えてください。
A1_6
強度低下の原因としては、「表面性状」「寸法効果」「切欠き効果」「残留応力」「環境効果」「異方性」「不均質(材質)」「不均一(応力)」などが考えられます。「表面性状」は材料表面の仕上げの状態などのことです。「環境効果」とは、材料の置かれている環境要因のことです。「異方性」「不均質」は下図のようになります。異方性とは試験片の採取方向によって材質が異なること、不均質とは試験片の採取位置が板厚表面か板厚中心部かによって材質が異なること、不均一とは、右図のように、みかけ上同じ力がかかっているはずなのに、実際には3本のそれぞれにかかる力が異なることをいいます。

■代表的な破壊の種類■
Q2_1
なぜカップ&コーンの形状の破面になるのですか?
A2_1
たとえば、丸棒試験片の場合、均質材であるとはいっても、厳密にはそうではなく、とくに引張強さを過ぎた点で、一番弱い断面で大きく変形し始めます。 軸中心部では、介在物との間に分離が起こり空洞を形成しつつ真っ直ぐに伸びますが、軸周辺部では、主にせん断によるすべり変形を伴い、最終的には分離するので、カップ&コーンの形状となるわけです。

Q2_2
「等軸ディンプル」と「伸長形ディンプル」の違いはどうして出てくるのですか?
A2_2
丸棒試験片において、「等軸ディンプル」は、軸中心部に、また「伸長形ディンプル」は、軸周辺部に認められます。前者は、破面鉛直軸に対称であり、後者は、せん断力の加わった方向に長く伸ばされています。それらは、それぞれの形成機構から明らかでしょう。

Q2_3
破面写真のA点とB点に注目したのはなぜですか?
A2_3
破面写真のA点は、軸中心部で「等軸ディンプル」が、B点は、軸周辺部で「伸長形ディンプル」が認められると判断したからです。

Q2_4
シャルピー吸収エネルギー遷移曲線からどのようなことが分かるのですか?
A2_4
シャルピー吸収エネルギー遷移曲線は、横軸に試験温度を、縦軸にシャルピー吸収エネルギー量を、それに加えて、縦軸にぜい性破面率もあわせて示すのが普通です。一般的に、温度が高い場合は、延性破面率が多く、温度が低くなるに従って、ぜい性破面率が多くなり、シャルピー吸収エネルギー量も著しく低下してきます。すなわち、構造物の破壊を考えた場合、ぜい性破壊で壊れる場合は極めて小さいエネルギーで壊れることになります。それゆえ、上記の遷移曲線から、どの程度の温度以上で使用すれば安全であるのかが推定できるのです。

Q2_5
なぜ「シェブロン・パターン」のような模様ができるのですか?
A2_5
ぜい性破壊を起こす場合、金属の結晶粒単位では、ある特定の面(へき開面という)が割れやすいことが明らかになっています。それらの面は、フラットなので、マクロ的にみれば、ギラギラした粗い面のように見え、き裂の伝ぱ方向に沿って広がった形をしています。その形状から、山形模様(シェブロン・パターン)またはヘリングボーン・パターン(にしんの骨形状)とも呼ばれています。

Q2_6
ぜい性破壊が原因で発生した事故はあるのですか?
A2_6
もっともよく知られた例として、第二次大戦中米国で大量に生産された全溶接の戦時標準船のうちの約250隻が致命的破壊を起こし、そのうち約10隻は、静かな湾内で停泊中に真っ二つに割れるという劇的な結果となった事例があり、その原因として、溶接技術に問題があったといわれています。溶接技術が格段に進歩した現在ではこのような心配は解消され、通常、疲労き裂が発生・進展し、最終的にぜい性破壊に至る場合がほとんどです。

Q2_7
疲労破壊の破面が比較的滑らかな面になるのはなぜですか?
A2_7
通常、疲労き裂は、応力集中部のごく狭い領域にせん断応力の繰返しにより発生します。次に発生した微視的き裂の先端部に塑性変形が蓄積され、き裂が徐々に進展していきます。いずれも塑性変形領域がミクロオーダーであるために、破面には肉眼的観察では塑性変形は認められず、比較的滑らかな面に見えます。

Q2_8
なぜ垂直応力に直角な面から45度傾いた面上に起点が存在するのですか?
A2_8
疲労き裂の発生過程を観察すれば、繰返し応力によりもっとも「滑りやすい面」で滑ることによって、微視的領域で変形が生じ、やがてその部分が微視的疲労き裂となっていくと考えられます。上記の滑りは、垂直応力に対し、45度方向に生ずる最大せん断応力に依存するので、45度方向の面上に疲労き裂がもっとも発生しやすいと考えられます。

Q2_9
き裂が伝ぱする部分のひし形のマークは何ですか?
A2_9
き裂の先端部にできる塑性変形領域です。この領域が引張応力と圧縮応力の繰り返しで溝状になり、き裂となって伝ぱしていきます。(レッスン3「疲労き裂伝ぱのモデル」参照)

Q2_10
疲労破壊が原因で発生した事故はあるのですか?
A2_10
著者が解析した242例の破損事例のうち、約80%は直接的に疲労破壊に起因しています。また、間接疲労の割合約10%を加えると、実に90%の例が疲労に起因しており、ほとんどの破壊事故は疲労に起因すると考えてよいでしょう。

Q2_11
結晶内の化学反応について詳しく解説してください。
A2_11
結晶内の化学反応に関しては諸説があり、ここではそのうちの代表的と思われるものを紹介しました。 遅れ破壊については、水素が関係していることが明らかにされ、別名「水素ぜい化割れ」ともいわれています。たとえば、局部腐食では水滴などが電気分解され、2H+が生じるとともに、Fe→Fe2++2e-となり、一方、2H++2e-→H2↑の反応が起こり、その結果結晶粒界で限界応力を超える圧力となって、破壊にいたると考えられています。

Q2_12
粒内破壊と粒界破壊はどのように見分けるのですか?
A2_12
結晶粒内では、原子は規則正しい配列を成しています。結晶粒界とは、ある結晶粒とその隣りにある結晶粒との境界を意味します。したがって、粒界では、原子の配列が乱れていたり、多少隙間もあります。金属の場合、常温では通常粒内から破壊しますが、特別な環境下では粒界から破壊する場合もあります。粒内割れと粒界割れは、意味が同じです。

Q2_13
粒界の三重点に応力が集中するのはなぜですか?
A2_13
高温時には、粒界強度が粒内強度よりも低下します。従って、外力を受けて、粒界で変形を吸収しようとした場合、粒界すべりが考えられます。この粒界すべりによって、結晶粒とその隣りの結晶粒との間に隙間が生じます。三重点などで応力集中が起こる場合も当然考えられます。

■疲労き裂の発生と伝ぱ■
Q3_1
「すべり線よりすべり帯のほうが黒っぽく見える」のはなぜですか?
A3_1
ここでは、すべり線は、静的引張の時に現れる模様で、すべり帯は、疲労の繰返し応力により現れる模様で、すべり線の集合体と判断できます。そのどちらの場合も塑性変形によるステップで構成されますが、前者よりも後者の方がこのステップの数がはるかに多いため、光学顕微鏡で観察した場合、光を反射しにくくなり、黒く見えるわけです。

Q3_2
ストライエーションの形成機構について詳しく教えてください。
A3_2
延性ストライエーションの場合で説明します。微視的き裂が発生し、伝ぱする過程を考えます。 まず、引張応力が加わることにより、このき裂が開口しつつ長さも伸びると同時にき裂先端では塑性域が形成されます。次に、逆方向の応力が加えられた場合、き裂の大部分は閉口しますが、き裂先端部ではその前の過程で発生した塑性域のために、完全には口を閉じないと考えられます。すなわち、横から見ると、山と谷が形成されるわけです。 これを繰返すので、山と谷の連続となり、き裂の破面側から観察すれば、鈍い円弧を描いた筋状の模様が認められることになります。

Q3_3
疲労限とは何ですか?
A3_3
疲労破壊を起こさない限界の最大応力のこと。図のグラフのaが疲労限で、これ以上の応力振幅であれば、繰返し疲労による破壊は起こりません。

Q3_4
△Kの意味について教えてください。
A3_4
Kは、応力拡大係数を指し、応力やき裂長さ、き裂の状態等に関連します。それに対して△Kは応力の変化に対応する量で、き裂の伝ぱ速度dl/dNは△Kに関連しています。

Q3_5
Φには工学的にどのような意味があるのですか?
A3_5
Φはき裂がどのような状態のところに存在するか、つまり丸棒なのか板なのかといった存在する状態によって決まる量です。

Q3_6
材料定数の工学的意味と、その関係式について教えてください。
A3_6
き裂伝ぱ速度dl/dNと応力拡大係数の範囲△Kとの間には、実験結果から直線関係が存在することをParisが発見し、パリス則とも呼ばれており、dl/dN=C(△K)mで表されます。これの両対数表示では、Cが縦軸との切片で、mが直線の勾配となります。

■疲労限と微視的停留き裂■
Q4_1
材料により疲労限の有無があるのはなぜですか?
A4_1
材料によって疲労限が存在したり、しなかったりする理由についての一般的な定説はないと考えられますが、これらに関する報告はいくつかあります。 たとえば、低炭素鋼の場合、疲労限の応力を107回繰返した平滑試験片には微視的停留き裂が存在することが明らかになっています。 すなわち、たとえき裂が発生しても、き裂先端部の抵抗の方が強ければ、き裂は伝ぱしないと考えられます。この微視的停留き裂が存在する理由として、き裂先端部の加工硬化、ひずみ時効硬化および局部的塑性変形等が挙げられています。加工硬化とはき裂発生時の塑性変形による硬化、ひずみ時効硬化とは、一定時間経過後、き裂先端部にあつまってくる炭素や窒素などによる硬化、局部的塑性変形とは、き裂先端部にかかる塑性変形です。 これらの影響により、き裂先端部には圧縮の残留応力が働くと考えられ、たとえき裂が発生しても、き裂先端部の抵抗のほうが強くなるので、き裂が伝ぱしないと考えられます。

Q4_2
微視的停留き裂のき裂の先端部の硬さが応力の繰返しによって硬くなるのはなぜですか?
A4_2
き裂の先端部では、塑性変形によって加工硬化し、それに伴うひずみ時効硬化も発生しているからと考えられます。

Q4_3
微視的停留き裂が認められない高マンガン鋼でも疲労限が存在するのですか?
A4_3
高マンガン鋼の場合、疲労限の応力を107回繰返した試験片に微視的停留き裂が存在するかしないかは、炭素量に依存します。 すなわち、著者等の研究では、その限界値は、0.15%程度であり、それ以下の炭素含有量であれば、微視的停留き裂は存在しないことを明らかにしています。なお、高マンガン鋼の場合、疲労限は存在しますが、炭素量によって微視的停留き裂が存在する場合としない場合があります。

■寸法効果■
Q5_1
寸法効果は、いろいろな種類の応力についてもいえることですか?
A5_1
寸法効果は、曲げや捩りおよび軸方向引張等の場合に認められます。 とりわけ、曲げモーメントの場合が顕著であり、とくに応力勾配の存在が指摘されています。

■破損解析の具体的手法■
Q6_1
破損解析から新技術あるいは新商品が開発された例を教えてください。
A6_1
「圧延機のタイロッドの破損解析例」から、ボルトの疲労強度を支配する4つの要因を初めて明らかにし、種々の対策と疲労強度向上効果との関係を定量的に評価することができました。これが、「新技術の開発」につながると考えられます。さらに、これらの結果から、疲労限が従来ボルトのものよりも約2倍も高い「CDボルト」が開発されました。これが新商品の開発の例です。なお、このCDボルトは、圧延機のタイロッドおよび関連部品、北九州市や大阪市の高速鉄道(モノレール)、JR東海のレール分岐器部等に使用され、好評を得ています。

Q6_2
PL法による世の中の変化の例を教えてください。
A6_2
PL(Product Liability)法(日本語では製造物責任法といわれる)が施行された結果、メーカー側からみれば、あらゆる場合を想定して製品を製造・販売する必要が生じ、不足の点は使用説明等で補完するように配慮されるようになってきています。電気製品等に「警告」あるいはWarning等のラベルが貼られているのを見かけるようになりましたが、これは使用者が不測の怪我等を被らないようにするためで、PL法に対する配慮でもあります。

Q6_3
フラクトグラフィとは何ですか?
A6_3
フラクトグラフィとは、破面解析学のことで、部材の破面や破面近傍の状態を肉眼や低倍率の拡大鏡、光学顕微鏡あるいは電子顕微鏡等を使用して解析することにより、破壊した原因等を特定する学問領域を意味します。

■身近な破損事例への適用■
Q7_1
0から までの積分が実行できない理由を教えてください。
A7_1
=0とおくと、定積分の結果で分母が0になる項が出てきてしまうので計算できません。

Q7_2
焼入れ・焼き戻し処理材とはどのような材料ですか?
A7_2
対象材料は、中炭素鋼以上の炭素量の多い鋼、低合金鋼やジュラルミンなどの金属材料で、焼入れとは高温に加熱して急速冷却処理すること、焼き戻しとは焼入れ処理した部材の内部ひずみを除去したり、あるいは靭性をつけるために、もう一度加熱・冷却することです。当然、焼き戻し処理の場合の温度は、焼入れ処理よりも低くなります。

Q7_3
疲労破面率が大きいと、変動応力を考慮しなくともよいのはなぜですか?
A7_3
疲労破壊面率が極めて大きいことは、材料の靭性が高いこともありますが、加えられた応力振幅が疲労限に近いことを意味します。その場合、変動応力が加わり、少数回でも疲労限よりもかなり高い応力が加わっていた場合、その高い変動応力の時に最終破壊してしまうことになるので、疲労破面率は大きくはならないことになります。 逆にいえば、疲労破面率が大きいと、材料の靭性が高いことも含めて、疲労限に近いほぼ一定振幅の応力が加わっていたと判断できます。

■破壊解析事例1■
Q8_1
メタルフローとき裂の進展の方向が一致するのが一般的なのでしょうか?
A8_1
メタルフローとは、写真の左右方向に出ている縞模様のことです。熱間圧延する前の素材にき裂が存在していた場合、その後の圧延工程でき裂が伸ばされます。この場合、メタルフローとき裂の方向が一致します。しかし、熱間圧延以降の製品にき裂が発生した場合、一般的にメタルフローの方向とは異なった方向にき裂が進展しています。このような状況から、どの工程でき裂が発生したのか推定することが可能です。

Q8_2
なぜ試験片はこのような形状なのですか?
A8_2
一般的に、試験片の形状は、試験機の能力、試験部から破壊させること等、いくつかの制約条件を満足させるようにして決定されます。

Q8_3
なぜき裂の伝ぱ速度としてストライエーションの間隔を使えるのですか?
A8_3
き裂伝ぱ速度dl/dNと応力拡大係数の範囲△Kとの間の実験式dl/dN=C(△K)mが成り立ち、Cおよびmは、材料定数であることをParisが発見しています。(JSME,Journal of JSME,vol.76,No.658(1973),1203) しかし、材料定数Cおよびmそのものには工学的意味はありません。なお、1回の繰り返しで1本のストライエーションが形成されると考えられます。

Q8_4
スミスの解を用いて換算すると、なぜ△KB=0.5△KAとなるのですか?
A8_4
A点は、ストライエーションの存在していた位置で,B点は計算上の評価位置です。き裂が半楕円状に伝ぱしたと仮定した場合、スミス(Smith)がA点とB点の応力拡大係数の値をそれぞれ計算し、図示しています。詳しくは文献を参照してください。(Journal Applied Mechanics,p957(1967,December))

Q8_5
初期き裂の深さを0.5mmとし、初期の欠陥のない状態から0.5mmのき裂が生じるまでの繰返し数を全繰返し数の約50%としているのはなぜですか?
A8_5
通常の疲労試験片の場合、肉眼またはルーペを使用して識別できるき裂長さは約1mm程度です。深さに換算すると0.5mmとなります。この程度のき裂が確認できる疲労寿命比は、応力振幅にもよりますが、経験的に50%程度であることが確かめられています。したがって概略経験値であるといえます。

Q8_6
このグラフの意味を教えてください。
A8_6
パイプの外表面には、圧縮の繰返し応力が加えられており、同時に引張の残留応力も存在しています。両者を重ね合わせると、引張・圧縮の両振応力状態になり、き裂が発生・伝ぱすることは十分に考えられます。 すなわち、見かけ上押し付け荷重のみ加えられていて、き裂が発生・伝ぱしにくいように見えても、実は応力的には両振応力状態であって、パイプの外表面からもき裂が発生・伝ぱしている事実をうまく説明することができます。

■破壊解析事例2■
Q9_1
なぜ、アークストライクが破壊の起点といえるのですか?
A9_1
破面の観察から、アークストライクが破壊の起点になっていることがわかります。

Q9_2
SCM440がアークストライクに弱い理由は何ですか?
A9_2
SCM440は、中炭素・低合金鋼で、炭素等量Ceq=0.809とかなり高い値となっています。かかる材料にアークストライクをつけると、とくに熱影響部では硬さが高くなり組織的にもぜい化してしまいます。しかも、アークストライクの下部にはビード下割れが発生しているので、曲げ荷重により簡単にぜい性破壊を起こしてしまいます。このような溶接部に発生する割れは炭素量以外にも合金成分が影響し、これらの成分の影響度合いを加味して求めた値が炭素等量Ceqです。

■破壊解析事例3■
Q10_1
「菊の花状の模様」ができるのはなぜですか?
A10_1
この軸は、段付きとキー溝付きの二重切欠きをもっており、繰返し捩り応力により、この二重切欠き部からき裂が発生し、まずはそれが周辺部に進展し、さらに内部へも進展して、最後に軸中心部付近で最終破壊に至っています。このような破壊形式のために、破壊面は菊の花状の模様となって見えると考えられます。

Q10_2
肉盛り溶接と、その影響について教えてください。
A10_2
肉盛り溶接される材料にもよりますが、肉盛り溶接することにより、その部分に溶接割れが発生したり、あるいは熱影響部がぜい化した組織になったりするので、注意を要します。とくに、溶接割れが発生していると、その後の部材の使用に支障が生ずるので、どうしても肉盛溶接をしなければならない場合は、専門業者に依頼し、製品検査を行っておくべきでしょう。

Q10_3
なぜβがβ1とβ2の掛け算になるのですか?
A10_3
経験則です。たとえば[Fatigue Sstrength of Structural Steel with Double Notches],Nishida et al,1999,689-693,International Conference on ADVANCED TECHNOLOGY IN EXPERIMENTAL MECHANICSなどを参照。

Q10_4
「最大捩り応力は定格トルクの1.5倍程度」なのはなぜですか?
A10_4
この場合は、クレーン軸ですが、クレーンを駆動させようとした場合や急に停止させようとした場合、定格トルク以上の力が軸に加わることは周知の事実です。最大捩り応力は、定格トルクの1.5倍程度加わっているというのは経験的数値に基づいています。

Q10_5
それぞれの対策について詳しく教えてください。
A10_5
「段付部からキー溝を離す」のは、段付部とキー溝との応力干渉をなくすることにあります。そうすれば、二重切欠き部の切欠き係数βは、段付部かあるいはキー溝のどちらか大きい方の切欠き係数のみの影響を考えればよいことになり、ずいぶん小さくなります。また、「切欠き半径を大きくする」は、段付部の切欠き半径を大きくすることにより、切欠き係数β1を小さくしようとする考え方で、これによる効果はそれほど大きくはありません。 さらに、「表面仕上げを良くする」は、とくに破壊した断面近傍、すなわち、段付R部やキー溝R部の表面仕上げをよくすることによりβ1やβ2を小さくするねらいがあります。

Q10_6
仕上げ精度を上げると、なぜ疲労限が約20%も向上するのですか?
A10_6
仕上げ精度は、加工コストに直接影響し、コスト低減の意味からできるだけ仕上げ精度は粗いままで使用するほうが安上がりです。そのために、とくに指定されない限り、このような大物の軸の場合、粗仕上げのまま使用する場合が多くなります。一方、疲労き裂の発生は、このような表面の微細な凹凸に強く影響され、凹凸が小さいほど、すなわち表面仕上げが良いほど、疲労限が向上するので、仕上げ精度を粗仕上げから、たとえば研磨仕上げに変更することにより、疲労限が20%程度向上することになります。

■破壊解析事例4−事例■
Q11_1
なぜ疲労限が60分の1程度に低下してしまったのですか?
A11_1
圧延機のタイロッドは、直径約500mm, 長さ14,000mmという極めて巨大なボルトで、疲労強度を支配する4つの要因のうち、とりわけ加工精度→片当りが大きく影響している可能性があります。というのも、ボルトのおねじとナットのめねじは通常別々の工程で加工されます。それゆえ、たとえ見かけ上同じピッチに揃えていても、まったく同じピッチに加工されているとは限りません。すなわち、巨大ボルトとナットを組み立てた場合片当りしやすくなるのです。このような問題を緩和するために、現実的には、同じ旋盤の同じ箇所を使用して同じピッチでボルトとナットのねじ加工を行っています。

Q11_2
なぜこの写真からき裂の方向がわかるのですか?
A11_2
この図のように、疲労により徐々に破損していき、最後に瞬間的にぜい性破壊を起こしていることから、き裂の伝ぱ方向が左から右であることがわかります。

Q11_3
なぜ疲労破面率が高いと、繰返し応力がボルトの疲労限に近いといえるのですか?
A11_3
このグラフのように、疲労限に近い応力振幅で破壊した場合、破面の疲労破面率は高くなります。
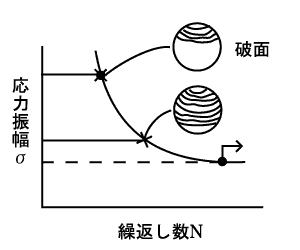

Q11_4
設計では繰返し応力が発生しないはずのボルトがなぜ疲労破壊したのですか?
A11_4
研削グラインダー取り付けボルトには、見かけ上繰返し応力は加わってはいません。しかし、その使用状況を検証すれば、砥石車と電動機とのあいだはベルトで連結されており、砥石車は、鋼片(ブルーム、ビレット)疵除去作業時に、鋼片と接触し衝撃や振動が伝わっています。その振動が、ベルトを通じて固定ボルトに加えられ、疲労破壊したものと推定されます。

■破壊解析事例4−まとめ■
Q12_1
ボルトの疲労寿命を長くするには、《材質を軟質材にする》、《オスとメスの締め付けている位置をずらす》とありますが、そうするとなぜ疲労寿命が長くなるのですか?
A12_1
ボルトの疲労強度を支配する要因の一つに、加工精度→片当たりを挙げることができます。いうまでもなく、ボルトは、おねじとめねじとの接触により、荷重を伝えています。 実際の接触は、みかけの接触よりもはるかに少ない面積であり、局部的に接触(片当り)しており、硬い材料ほどその傾向が顕著であるといわれています。したがって、壊れにくいめねじ側に軟質材を使用することで、片当りを緩和しようとするねらいです。また、ボルトの位置をずらす意味は、疲労破壊は、ナットの端面部に限定されるので、ある期間使用した後に、その危険断面の位置をずらすことで、延命策を施すものです。

Q12_2
「応力の流れ」とはどのようなことですか?
A12_2
ここでは、ボルトに引張応力が加えられ、それがナット側に伝わる状況について説明します。ボルトの円筒部に加えられた引張応力は、おねじからめねじへと伝えられますが、目には見えません。そこで、同じ形状のものについて「水の流れ」を想定すれば、どの部分でもっとも応力集中の程度が顕著となるか、具体的に理解できるようになります。すなわち、水の流れを利用して、応力の伝わる状況(流れ)を理解しようとする方法です。

Q12_3
それぞれの材質の特徴などを説明してください。
A12_3
SCM440は、中炭素鋼に1Cr-0.2Moが含まれており、SNCM630は、中炭素鋼に3Ni-3Cr-0.6Moが含まれた低合金鋼で、S20Cは低炭素鋼です。詳細は、JIS規格表を参照してください。

Q12_4
このような形状にすると荷重分布が均一になるのはなぜですか?
A12_4
ボルトの疲労強度を支配する主な要因として、荷重分担が不均一、引張と曲げの応力集中、および加工精度→片当りがあります。不完全ねじ部を除去する程度に細くし、勾配をつけて完全ねじ部へとつなぐような形状に加工することにより、これら4つの要因のすべてについて、緩和または均一化させることにより疲労限が大幅に向上します。つまり、ボルトのねじ山部の漸減研削により、ナット端面側ではたわみやすいナットねじ山先端部で接触することにより荷重分担が均一化、引張りと曲げの応力集中が緩和します。さらに、たわみやすいナットのねじ山先端部で接触するので、とくにナット端面付近では、たとえ片当りが発生しても、それが緩和されます。
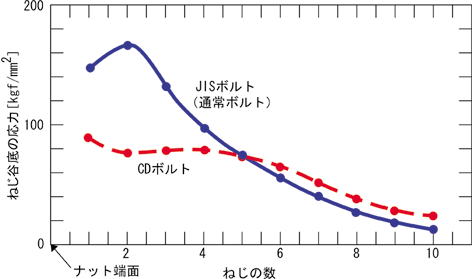

|