 |
■1. 設計開発の流れにおける設計品質■
Q1.国際標準となるプロジェクトマネジメントが設計業務になぜ必要か。
Q2.顧客満足を得るために、設計者は具体的に何を考慮しなければならないのか。
Q3.フロントローディングは製品の品質を良くすることができるのか。
Q4.デザインレビューは、製品設計においてなぜ重要か。
Q5.設計手法を学ぶためにはどのようなやり方があるのか。
■2. 顧客満足を設計に反映する品質機能展開■
Q6.品質展開を行うチームはどの様な能力がある人が適していますか?
Q7.要求品質の抽出のあと品質要素を抽出してその後品質特性になるのでは?
Q8.数値評価は1〜5点でないといけないのですか?
Q9.重要度評価方法はアンケートのほかにどのような方法がありますか?
Q10.品質展開の重要度は社会環境、自社の技術力とともに変わるものですか?
■3. 設計課題解決案創出するTRIZ■
Q11.TRIZの矛盾による解決方法は独特なものでしょうか。
Q12.TRIZを使えば、ただちに技術問題を解決できるのでしょうか。
Q13.矛盾マトリックスの各セルに複数の「40の発明原理」の番号が示されていますが、すべて問題解決に適用できるのでしょうか。
Q14.技術的矛盾の考え方で、改善したい特性と改善によって悪化する特性についてもっと知りたいのですが。
Q15.技術的矛盾がない場合も矛盾マトリックスは適用できますか。
Q16.TRIZを本格的に勉強したいのですが、ステップを教えてください。
Q17.コンピュータを活用しないでも、TRIZを利用できるでしょうか。
Q18.TRIZ以外に技術問題解決の手法があれば紹介していただけませんか。
■4. 要求機能を安定的に実現するタグチメソッド■
Q19.実験をするのに何故誤差因子を考える必要があるのですか。
Q20.直交表で交互作用は見なくてもよいのですか。
Q21.何故品質特性(クレームや検査項目など)を評価指標にしてはいけないのですか。
Q22.誤差因子が増えた場合どのように解析しますか?
■5. 多次元データを活用するMTシステム■
Q23.MT法を実施する場合、項目数およびサンプル数はどのくらい必要ですか?
Q24.MT法で、対象サンプルのマハラノビス距離が、どのくらいの値から単位空間とは違うものと判断するのでしょうか?
Q25.MT法で、項目間の相関が強く、マハラノビス距離を求める際に、相関行列の逆行列が求められません。どうしたら良いでしょうか?
Q26.単位空間をつくる場合に、計測できなかったサンプルが発生したり、データを紛失する場合があります。このように欠測値が出た場合、どうしたら良いですか?
Q27.多次元データから正常・異常を診断する方法に、多変量解析の判別分析があります。MT法と判別分析は何が違うのでしょうか?
■6. プロジェクトマネジメント■
Q28.製品ライフサイクルの短期化についておしえてください。
Q29.PMBOKについてもう少し詳しく教えてください。
Q30.日程計画には、大日程計画・中日程計画・小日程計画の3つがあるそうですが、必ず3つ作成
しなければいけないのですか。
Q31.リスク分析やリスク評価は必ず行う必要があるのでしょうか。
■1. 設計開発の流れにおける設計品質■
Q1
国際標準となるプロジェクトマネジメントが設計業務になぜ必要か。
A1
ものづくりの製品やサービス業の新規開発は国際的な競争においても成果を出すことが期待されています。今日のグローバルビジネスにおいては、製品の質のみならず経営全体の仕組みについても市場から認められる必要があり、設計業務プロセスも対象です。即ち、顧客指向、経営の質が伴って製品やサービスの実現に伴う設計業務が評価されるのです。このような背景の下、国際標準となるISO9001やプロジェクトマネジメントが共通の仕事の仕方として必要になります。

Q2
顧客満足を得るために、設計者は具体的に何を考慮しなければならないのか。
A2
製品設計において、その専門技術の知識や経験が不可欠です。しかし、技術力だけでは、市場が求める、顧客が欲しいと考える製品をヒットさせることは難しい場合が多くなっています。 いわゆるマーケットインといわれる顧客が求めるものはどのような製品なのかといった『声』を知ることが必要です。品質機能展開の手法を用いると、このような品質情報を解析することができます。

Q3
フロントローディングは製品の品質を良くすることができるのか。
A3
製品の品質は開発段階において品質リスクの低減活動により確保できます。新製品を開発する場合、全く新しい技術のみを使うとすれば製品の実現や品質信頼性のリスクが高くなります。リスクの課題を企画段階で分析し洗い出し、夫々の課題を設計の初期段階に明らかにすることが品質のフロントローディングといえます。量産導入までの時間があれば設計上の対策、生産技術の対策が検討できるのでフロントローディングにより製品品質は確保できます。

Q4
デザインレビューは、製品設計においてなぜ重要か。
A4
デザインレビューにおいて確認漏れが残る、言い換えれば設計内容が不充分であると工程設計、生産状態に移ったとき設計変更が生じます。これは、開発納期の遅延と開発費の増加を招き、企業や組織に対し顧客の喪失や経済的損失をもたらします。従って、デザインレビューは製品開発の流れにおいて常に改善を進め、失敗事例をよく分析しその実施手順を継続的に改善することが重要です。

Q5
設計手法を学ぶためにはどのようなやり方があるのか。
A5
設計手法は、品質管理手法、各種技法に関する書籍があります。これらを学習したり資格試験に挑戦するプロセスで知識を習得できます。さらに所属する会社の日常業務の課題解決で実際に使ってみることが肝要です。そして、職場内の上司、同僚と議論しながら経験を積むことが有効です。また、社外の研究会、学会などにおける活動に参加することでより応力を身につけることができます。

■2. 顧客満足を設計に反映する品質機能展開■
Q6
品質展開を行うチームはどの様な能力がある人が適していますか?
A6
原始データ収集段階では、製品の使用現場を熟知している、問題意識を持っている人材が必要です。要求品質に変換するときはボキャブラリーの豊富な人が良いと思います。品質特性を抽出する段階では、品質特性の知識、検査・試験、評価方法に知識がある人、品質企画設定の段階では、全部門からある程度長期的なものの見方ができる人材が求められます。

Q7 要求品質の抽出のあと品質要素を抽出してその後品質特性になるのでは?
A7
その通りです。要求品質の代用特性である品質要素を抽出します。その後定量可能な品質特性とします。今回のレッスンでは品質特性という言葉を使いました。測れないものは改善できない(You cannot improve you cannot measure.)といわれています。

Q8
数値評価は1〜5点でないといけないのですか?
A8
1〜3点でも,2点・3点・4点でも、1〜10点でもかまいません。

Q9
重要度評価方法はアンケートのほかにどのような方法がありますか?
A9
例えばAHP(Analytic Hierarchy Process;階層化意志決定法)法があります。AHP法は米国ピッツバーグ大学T.Lサーティー教授が米国の政府機関で数理計画法の開発や応用をした経験から、トップの意志決定者が抱える構造が不明確で複雑な問題を扱えるモデルや方法はないかと考えて開発した方法です。

Q10
品質展開の重要度は社会環境、自社の技術力とともに変わるものですか?
A10
その通りです。よって、最初から「完璧さ」を求めず、データベースとして活用し都度更新する使い方もあります。また、社会環境、自社の技術力と共にボトルネック技術も替わって行きます。

■3. 設計課題解決案創出するTRIZ■
Q11
TRIZの矛盾による解決方法は独特なものでしょうか。
A11
技術問題の解決に「矛盾」を扱ったことは、革新的なものといえます。しかし、矛盾を扱う分野は他にないわけではありません。たとえば、資金運用のポートフォリオ理論では、リターン(運用益)とリスクのトレードオフ関係をうまく利用し、最適ポートフォリオを実現しようとするもので、広くみれば目新しいものではありません。また、企業の中には、「矛盾」を取り込んで事業革新をスパイラル的に展開し、コンピューター分野のリーディングカンパニーの地位を築いてきた企業の例もみられますので、「矛盾」というキーワードは、技術革新のポイントといえるかもしれません。

Q12
TRIZを使えば、ただちに技術問題を解決できるのでしょうか。
A12
TRIZを使えば、ただちに問題を解決できるわけではありません。解決策のヒントを与えてくれるツールと理解してください。

Q13 矛盾マトリックスの各セルに複数の「40の発明原理」の番号が示されていますが、すべて問題解決に適用できるのでしょうか。
A13
各セルに示された番号の全てが適用できるわけではありません。目標とする問題解決に合っていなければ、除外し、当てはまりそうなものを選択します。なお、各セルに示される番号は、番号の並びが不規則です。これは、最初の方の番号を優先することを意味しています。たとえば、タテの14番とヨコの02番をみると、40、26、27、01と番号の並びが不規則です。この場合、40番の発明原理が優先されることを意味しています。しかし、目標とする問題解決に当てはまるとは限りませんので、次の番号があてはまるかどうか順に見ていきます。
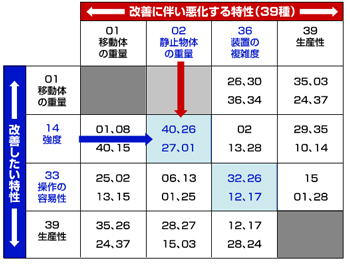

Q14 技術的矛盾の考え方で、改善したい特性と改善によって悪化する特性についてもっと知りたいのですが。
A14
テイクアウト用コーヒー容器の事例で紹介しますが、「紙容器はつぶれやすい→改善したい特性は「つぶれない」ことで、具体的には「紙厚をアップする」ことが考えられます。これに対して、悪化する特性は「素材使用量が増える」などが悪化する特性になります。これが矛盾の関係です。つまり改善したい特性と改善することによって、悪化する特性の矛盾関係から問題解決のヒントを得て、アイデアを絞り込んでいく考え方です。なお、改善したい特性と改善することによって悪化する特性は、39の技術特性に当てはまりやすい特性に具体化していくことがポイントです。

Q15
技術的矛盾がない場合も矛盾マトリックスは適用できますか。
A15
実際の場面では、技術的矛盾がない場合や、あるいはどうしても特定できないケースがあり得ます。そのような場合は、矛盾マトリックスが使用できませんので、直接、「40の発明原理」から入り、アイデア出しすることもできます。

Q16
TRIZを本格的に勉強したいのですが、ステップを教えてください。
A16
まず、(1)矛盾マトリックスを理解し、自分自身で活用し、実際に体験することが重要です。次に(2)イフェクツ、3番目に「物質−場分析」にステップを踏んでいくことがよいと思います。職場などで組織的に実践していくためには、技術者だけの理解だけでなく、技術系の上席管理者の理解も大切となります。他の手法についてもいえることですが、いわゆる「食べず嫌い」は最も避ける必要があります。

Q17
コンピュータを活用しないでも、TRIZを利用できるでしょうか。
A17
TRIZの提唱者であるアルトシュラーの時代には、今のようにコンピューターが普及していなかったこともあり、紙と鉛筆で行っていましたので、コンピューターを利用しないでも使用できます。しかし、逆引き辞典であるイフェクツのように膨大な情報を検索する場合は、コンピューター利用が欠かせません。

Q18
TRIZ以外に技術問題解決の手法があれば紹介していただけませんか。
A18
40の発明原理の考え方に近いものとして、ブレーンストーミングの提唱者で知られるオズボーンのチェックリストやP&Pネットワークが提唱するバラバラ化チェックリスト、製品の潜在力チェックリストなどがあります。特許など知財管理教育の場で、しばしば照会される手法です。このような手法に目を向けてみることは、TRIZへの理解が早まるかもしれません。

■4. 要求機能を安定的に実現するタグチメソッド■
Q19
実験をするのに何故誤差因子を考える必要があるのですか。
A19
製品に求められるのは機能であり、この機能がユーザーの様々な使用や環境条件によって安定していることが良い製品といわれてます。しかし、メーカーでは、ユーザーの様々な使用や環境条件を指定したり、制御したりするのは事実上不可能です。従って、製品設計段階では、想定されるバラツキの原因となる因子を積極的に実験に組み込んで、製品機能が安定化する条件を見つけることが大切です。

Q20
直交表で交互作用は見なくてもよいのですか。
A20
L18直交表では他の直交表と異なり、内側に割付けた制御因子同士の交互作用が特定の列に出ないようになっています。従って、パラメータ設計では、直交表の内側に割付けた制御因子と外側に割付けた誤差因子との交互作用を評価します。この交互作用が小さくなる条件を見つけて市場における製品機能の安定化を図ります。

Q21
何故品質特性(クレームや検査項目など)を評価指標にしてはいけないのですか。
A21
品質特性は、本来製品に求められる機能(仕事)の結果です。従って、品質特性値で評価しようとすると数が多くなり、それだけ総合的に最適化していくのが難しく、効率が落ちるからです。

Q22
誤差因子が増えた場合どのように解析しますか?
A22
誤差因子が増えた場合でも、その出力に対する効果について出力を上げる又は下げるといった定性的傾向がわかる場合は、出力を上げる条件と出力を下げる条件に誤差因子を調合して2水準にまとめることになります。しかし、定性的傾向が分からない場合は、誤差因子を新たに直交表の外側に割付け、内側に割付けた制御因子との直積で解析を行います。

■5. 多次元データを活用するMTシステム■
Q23
MT法を実施する場合、項目数およびサンプル数はどのくらい必要ですか?
A23
マハラノビス距離(MD)を求めるには相関行列の逆行列を求める必要があります。そのためには、行列計算の制約でサンプル数は項目数より多くないと計算できません。また、安定した結果を得るには、サンプル数は項目数の3倍は必要です。
必要な項目数は、まずは、できるだけ違う観点の項目についてデータを集め、正しく検査・診断できるようにします。その後、項目選択で必要な項目に絞り、検査・診断のコストや時間を削減する進め方が適切です。

Q24
MT法で、対象サンプルのマハラノビス距離が、どのくらいの値から単位空間とは違うものと判断するのでしょうか?
A24
マハラノビス距離は多次元空間のばらつきの尺度です。一次元データにおける、標準偏差(σ)と同様に捉えれてください。一次元で3σを超えたものが異常と判断するように、マハラノビス距離では、3〜5を超えた場合は、違う集団のモノと捉えます。

Q25
MT法で、項目間の相関が強く、マハラノビス距離を求める際に、相関行列の逆行列が求められません。どうしたら良いでしょうか?
A25
MT法では、項目間の相関を積極的に使うことで、パターン認識できるようにするのが特徴です。しかし、項目間の相関が強い場合、相関行列の逆行列が求められなくなります。
その場合は、やむをえず、どちらか一方の項目を使い、もう一方は項目から除きます。
なお、MT法は逆行列を使いますが、T法の場合は逆行列を使わないため、この問題は起きません。

Q26
単位空間をつくる場合に、計測できなかったサンプルが発生したり、データを紛失する場合があります。このように欠測値が出た場合、どうしたら良いですか?
A26
ある項目について、1つでも値がないサンプルが発生すると、その項目は解析に使えなくなってしまいます。それでは、もったいないので、次のような救済策をとります。
・データが取れている他の全サンプルの平均値を欠測値に代入する。
・時系列データで、欠測値の前後の値がわかっている場合は、補間する。

Q27
多次元データから正常・異常を診断する方法に、多変量解析の判別分析があります。MT法と判別分析は何が違うのでしょうか?
A27
MT法では、正常な集団を単位空間に定義し、単位空間から対象サンプルまでの距離が大きいものは異常と判断する考え方です。一方、判別分析は、正常な集団と異常な集団の2つの集団を定義し、対象サンプルが正常な集団と異常な集団のどちらに近いかを求めます。
MT法は多様な異常に対する診断に対応しています。
判別分析は典型的な異常と正常を見極めるのに有効なので、使い分けが必要です。

■6. プロジェクトマネジメント■
Q28
製品ライフサイクルの短期化についておしえてください。
A28
わが国での高度成長期においては、大量生産・大量消費のパラダイムのもとに、品質の良い製品を安く生産することが重視されていました。
しかし昨今では、技術革新のスピードが速くなり、市場には新製品が次々に登場し、最新型の製品が旧型になるまでの期間がますます短くなっています。
また、各種メディアによる情報が氾濫し日々変化する状況においては、消費者の嗜好も大きく影響を受け、いわゆる「ヒット商品」も、瞬く間に過去の物となってしまうことも少なくありません。
また、消費者の嗜好そのものも多様化しており、メーカーは様々な製品を次々に市場に提供して消費者の反応を伺いながら、注力すべき製品を検討しています。このような背景が、製品が市場における寿命である製品ライフサイクルの短期化につながっているのです。

Q29
PMBOKについてもう少し詳しく教えてください。
A29
PMBOKは、国際的に標準とされているプロジェクトマネジメントの知識体系(ガイド、手法、メソドロジー、ベストプラクティス)であり、建設、製造、ソフトウェア開発などを含む幅広いプロジェクトに適用できるプロジェクトマネジメントの基盤を提供する。
PMBOKはプロジェクトマネジメント協会(PM協会、Project Management Institute、PMI)が、PMBOKガイド(A Guide to the Project Management Body of Knowledge、PMBOK Guide)として提供しており、最新版は第4版である。またPMI本部が認定するプロジェクトマネジメントの国際資格に、PMP(プロジェクトマネジメントプロフェッショナル)がある。日本にはPMI日本支部がある。

Q30
日程計画には、大日程計画・中日程計画・小日程計画の3つがあるそうですが、必ず3つ作成
しなければいけないのですか。
A30
必ず3つ作成しなければいけないということはありません。特に小規模のプロジェクトなどでは、
大枠の日程計画と詳細な日程計画の2種類である場合もあります。

Q31
リスク分析やリスク評価は必ず行う必要があるのでしょうか。
A31
可能な限り行う方が良いですが、必ずしも行う必要はありません。
リスク特定を含め、リスク分析やリスク評価は、最終的には優先順位の高いリスクに対してリスクの低減や削減等の対応を検討するために行います。リスクの取りこぼしが無いように、また合理的に検討を行うために、これらの作業は重要と言えます。しかし、これらの結果から導かれる優先順位の高いリスクや対応は、現場を良く知っている専門家等の話し合いの中で導かれる結果と同じ場合や、予めある程度分かっている場合もあります。時間や費用の面等から、リスクマネジメントの基本フレームに沿って検討が困難な場合には、フレーム通りに行わない場合もあり得ます。


|
|
 |