1. 化学安全管理の概論
Q1.化学プラントは運転員や協力会社の従業員などプラントの現場で作業する人が安全確保に大きな貢献をしていると思いますが、なぜトップマネジメントの安全に対する姿勢が重要なのですか。
Q2.プロセス危険性評価はどのようなときに実施したらよいですか。また、評価手法としてどのようなものがありますか。
Q3.なぜ変更管理が必要なのですか。
Q4.危険予知訓練と危険予知活動の違いは何ですか。
Q5.安全監査の目的と監査にあたっての留意点は何ですか。
2. 危険評価技術(HAZOP)
Q6.化学プラントの事故は、プロセス変動によるものだけでなく、設備の腐食や劣化によっても発生していますが、HAZOPはそれら腐食、劣化による事故防止にも適用できますか。
Q7.HAZOPをプロセスフロー図を対象として実施しようと思いますが、それで良いでしょうか。
Q8.ずれの原因となる機器故障や誤操作をスタディノードの中に特定したら良いのは何故ですか。
Q9.HAZOPにおけるずれ想定にあたってする重要なプロセスパラメータは何ですか。
Q10.HAZOPにおいてプラントへの影響検討にあたり講じられている安全対策を考えないのは何故ですか。
Q11.HAZOPでの検討結果の記録にあたっての留意すべき点はなんですか。
3. 設備安全技術
Q12.化学プラントの安全確保にあたっては、何故、事故の予防と被害の拡大防止という両面から安全対策を講じることが必要なのですか。
Q13.フェールセーフと安全インターロックの違いは何ですか。
Q14.安全インターロックを定期的に点検する必要があるのは何故ですか。
Q15.安全弁と破裂板の目的と使用場所の違いはありますか。
Q16.装置から可燃性ガスや毒性ガスの漏洩を検知するための定置式漏洩検知設備と携帯式漏洩検知器の役割の違いは何ですか。
Q17.ドミノ効果とは何ですか。また、化学プラントにおいて火災発生時のドミノ効果を防止するためにどのような対策を行っていますか。
4. ヒューマンファクター
Q18.ヒューマンファクターとヒューマンエラーは、どう違うのですか。
Q19.スリップとミステイクの違いがよくわかりませんが、どのように違うのですか。
Q20.ヒューマンファクターのモデルとしては、m-SHELモデルのほかに何がありますか。
Q21.ヒューマンエラーが発生して困っています。何か抜本的な対策はありませんか。
Q22.チームエラーを防止するための訓練方法とは何ですか。
5. リスク解析技術
Q23.化学プラントは大量の危険物質を取り扱っているのでリスクは高いと考えるのでしょうか。また、リスクを小さくするには何が必要ですか。
Q24.危険源の特定にあたって、複数のメンバーからなるチームで検討を行うのは何故ですか。
Q25.What-if、HAZOP、故障モード影響解析、フォールトツリー解析、イベントツリー解析はいつ頃から使用されたのですか。
Q26.リスク解析にあたり、What-if解析、HAZOP、故障モード影響解析、フォールトツリー解析、イベントツリー解析はどのような使い分けとなるのでしょうか。
Q27.フォールトツリー解析においてブール代数を使ってツリーを整理していきますが、ブール代数において、A+A=A、A・A=Aという関係式がありますが、これはどういう意味ですか。又、何故そのようになるのかを分かりやすく説明してください。
Q1
化学プラントは運転員や協力会社の従業員などプラントの現場で作業する人が安全確保に大きな貢献をしていると思いますが、なぜトップマネジメントの安全に対する姿勢が重要なのですか。
A1
化学プラントの安全確保にあたっては、プラントオペレータや設備管理担当者、工事や補修などの作業を行う協力会社の従業員など、実際に現場で働いている人たちが安全確保に大きな貢献をしているといえます。
しかし、企業という組織においてはトップマネジメントが経営ならびにプラントの安全確保にあたり全責任を負っているといえます。
現場の従業員はトップマネジメントの姿勢を注視しています。
トップマネジメントが安全を軽視したり、安全に対する姿勢が曖昧であれば、それは現場にも大きく影響し、事故の間接的な誘発要因になります。
このため、トップマネジメントは確固とした安全理念、安全基本方針を示し、全従業員に周知徹底させることが必要となります。

Q2
プロセス危険性評価はどのようなときに実施したらよいですか。また、評価手法としてどのようなものがありますか。
A2
プロセス危険性評価の実施時期としては、新規プラントの建設時、既設プラントの能力アップや改造時、原材料など取扱物質を変更したときなどに行うと良いでしょう。
また、建設してから長い年月がたった既設プラントの安全性を見直すためにも実施することも重要です。
プロセス危険性評価手法としては、プラントの潜在危険を洗い出すためのWhat-if、HAZOP、FMEAやプラントに起こって欲しくない危険事象がどのような原因の組み合わせで発生するかを解析するFTAなどの手法があります。
目的に応じてこれら手法を使い分けると良いでしょう。

Q3
なぜ変更管理が必要なのですか。
A3
プラントは運転条件や機器、触媒の変更、原材料など取扱物質の変更などのほか、プラント運転組織の変更や職場の配置換えによる人の変更など様々な変更が行われます。
変更前は安全な操業を行っていても、運転条件や触媒の変更、取扱物質の変更などにより今までとは異なった新たな危険要因が発生する可能性があります。
このため、変更によって新たな危険要因が考えられないかを検討・評価する必要があります。
また、組織や人員の変更により情報連絡ルートが異なったり、役割分担などが曖昧であると間接的な危険要因となります。
以上のように変更にともなう新たな危険性を把握し対策を講じるために変更管理が必要といえます。

Q4
危険予知訓練と危険予知活動の違いは何ですか。
A4
危険予知訓練は、危険性が潜んでいるイラストを使用し、作業における危険個所や危険行動を見つけ、その対策を考える訓練です。
一方、危険予知活動は、実際の作業開始前に、その日の作業内容や現場の状況にそって不安全状態や不安全行動によって起こる可能性のある災害を想定し、それに対する防止対策を講じることにより災害を未然に防ぐための活動です。
危険予知訓練は、現場での危険予知のために準備として事前に行うものに対し、危険予知活動は現場でその日の作業開始前に行うものとして区別できます。

Q5
安全監査の目的と監査にあたっての留意点は何ですか。
A5
安全監査は事業所における安全管理プログラムの整備状況ならびに実施状況が適切であるかを評価し、必要に応じて改善点を指摘するためのものです。
適切で十分な安全監査を行うにあたっては、監査体制、監査方法、頻度などに関する監査規程を策定しておくことが必要です。
また、監査体制を決めるにあたっては、監査実施者の能力、監査員の人数に配慮を払うほか、監査結果の公平性や客観性を維持するために被監査側と利害が関係しないよう留意することが必要です。

Q6
化学プラントの事故は、プロセス変動によるものだけでなく、設備の腐食や劣化によっても発生していますが、HAZOPはそれら腐食、劣化による事故防止にも適用できますか。
A6
HAZOPは機器故障などによって発生した正常状態からのずれがプロセス変動となって進展し、危険事象となって表面化するか否かを検討することにより事故の予防をはかる手法でプロセス危険性評価手法といえます。
設備の腐食や劣化はプロセス変動に起因することはまれで、主として経年変化によるものといえます。
設備の健全性維持にあたっては、定期的な保守点検プログラムなどによる設備管理に依存することになります。
しかし、熱交換器からの洩れで、冷媒または熱媒がプロセス流体に混入する場合や減圧系の洩れで空気がプロセス流体に混入する場合などのプロセス変動につながる想定にはHAZOPを用いることができます。

Q7
HAZOPをプロセスフロー図を対象として実施しようと思いますが、それで良いでしょうか。
A7
プロセスフロー図は、熱収支、物質収支、通常使用するラインや主要な機器は示されていますが、安全設備や配管のサイズなど詳細な情報はありません。
一方、配管計装系統図は安全設備をはじめ、プラント運転に必要なライン、制御システム、手動弁など詳細な情報が記載されています。
HAZOPはプラントを構成する機器の故障、オペレータの誤操作などを引き金としてずれ(プロセス異常)が発生したときに、それが危険事象にまで進展するのか否かの検討をおこないます。
このため、手動弁、制御システム、安全設備などが記載された詳細な図面である配管計装系統図を対象として実施するのが基本となります。
なお、プロセスフロー図は温度、圧力、組成など主要な運転条件を確認するために必要であり、プロセスフロー図も補完資料として使用されます。

Q8
ずれの原因となる機器故障や誤操作をスタディノードの中に特定したら良いのは何故ですか。
A8
流れのずれ、圧力のずれ、温度のずれなどの原因を検討対象範囲であるスタディノードの外側に見つけようとすると膨大な時間がかかるとともに、検討が発散する可能性があります。
ずれの原因を洗い出す範囲をスタディノードの中に限定することにより、焦点を絞り、効率よい検討が出来ます。
なお、ずれ発生時のプラントへの影響はスタディノードの外にでてもかまいません。

Q9
HAZOPにおけるずれ想定にあたってする重要なプロセスパラメータは何ですか。
A9
化学プラントの運転にあたり管理すべき基本となるプロセスパタメータは、流量、温度、圧力、液レベル、成分(組成)です。
この5つのパラメータのずれは必ず検討対象としたほうがよいでしょう。
なお、物質の濃度が管理すべき重要なパラメータであれば、それも検討対象とします。
すなわち、プロセスの特性を考慮して必要なパラメータを追加すると良いでしょう。

Q10
HAZOPにおいてプラントへの影響検討にあたり講じられている安全対策を考えないのは何故ですか。
A10
プラントへの影響検討にあたり、講じられている安全対策を考慮に入れると安全対策があるから問題なしという結論に達しかねません。
安全対策がないものとして影響検討を行うことにより、そのまま放置したら危険事象につながるのか、運転トラブルで収束するのかかが明らかになります。
安全対策を考慮せずに影響検討を行うことによりプロセス固有の潜在危険が明らかになります。
潜在危険を特定することにより、どのような安全対策を講じたらよいかが明らかになります。

Q11
HAZOPでの検討結果の記録にあたっての留意すべき点はなんですか。
A11
HAZOPの検討結果は、検討に使用した図面と付き合わせると第三者にも分かるように記録すると良いでしょう。
このため、検討対象となった機器には必ず機器番号をつけて記録します。
また、HAZOPにおいてはプラントへの影響検討が重要であり、このため、どのような経過を経て事象が進展するのかを、簡潔にかつ要領よく記録することが必要です。

Q12
化学プラントの安全確保にあたっては、何故、事故の予防と被害の拡大防止という両面から安全対策を講じることが必要なのですか。
A12
化学プラントは多数の機器から構成され、また、オペレータにより運転操作が行われる大規模システムです。
設計段階での機器選定や運転段階での保守点検などにより機器の健全性を維持するための作業が行われていますが、100%機器故障をなくすことには限界があります。
また、人間はエラーを犯す習性を持っています。
このため、事故を予防するための対策を第一に考えることは当然必要ですが、万一、機器の故障などにより事故が発生した際には被害の拡大を防止するという多重防護の考え方が必要になります。

Q13
フェールセーフと安全インターロックの違いは何ですか。
A13
フェールセーフは、機器に故障などが生じた場合にも、それに関連する系の安全性が損なわれないという考えです。
例えば、発熱反応器の冷却系の空気で開閉の動作をさせる調節弁では、空気が停止した場合には、弁が全開するように設定することがフェールセーフな設計といえます。
一方、インターロックは冷却水が何らかの原因で停止し、そのまま放置すると反応器の温度が上昇し反応暴走など危険事態が想定される場合に、温度の異常を検知して反応器の内容物を緊急に放出するために緊急抜き出し弁などを開放する安全システムを付加する考えです。
すなわち、フェールセーフは故障が発生しても系が安全な方向に故障するという考えに対し、インターロックは異常を検知して安全システムを作動させるという付加的なシステムといえます。

Q14
安全インターロックを定期的に点検する必要があるのは何故ですか。
A14
安全インターロックはプロセス状態が正常運転範囲を大きく逸脱したときに、異常を検知して事故防止のために自動で作動する重要な安全システムです。
また、安全インターロックは通常の運転状態では待機状態にあり故障が発生したとしても検知できません。
このため、定期的に点検を行い、システムが故障していないかを確認し、健全性を維持する必要があるからです。

Q15
安全弁と破裂板の目的と使用場所の違いはありますか。
A15
安全弁も破裂板も装置を過剰圧力による破壊から保護する圧力放出設備で目的は同じです。
なお、安全弁は装置の圧力が降下すると自力で閉じますが、破裂板は一度作動すると開放状態となります。
この特性を考慮に入れてどちらを採用するかが決められます。
なお、腐食性の強い流体、粘度の高い流体、ゴム状物質を保有している装置においては、安全弁が腐食されたり粘着質の物質の付着により作動しなくなる可能性があるため破裂板が使用されることが多くなります。
また、安全弁の腐食からの保護、粘着質の物質の付着による作動不良などを防止するために安全弁の入口側の配管に破裂板を設置して併用することもあります。

Q16
装置から可燃性ガスや毒性ガスの漏洩を検知するための定置式漏洩検知設備と携帯式漏洩検知器の役割の違いは何ですか。
A16
プラントは定期パトロールにより振動、異音、異臭、また目視などにより装置の異常や装置からの漏洩の有無をチェックしています。
この定期パトロールでの漏洩検知には携帯式漏洩検知器が用いられます。
しかし、常時パトロールを実施し漏洩の有無をチェックするには限界があります。
このため無人での漏洩検知をおこなうために定置式漏洩検知設備が利用されます。
定置式漏洩検知器は可燃性や毒性の液体やガスを保有している装置の周辺の、ガスの滞留しやすい場所に設置し、漏洩を検知したならばコントロールルームに警報が発せられ運転員に知らせます。
なお、携帯式漏洩検知器は、定置式漏洩検知器の警報が鳴ったときに漏洩個所の特定を行うなどのためにも使われます。

Q17
ドミノ効果とは何ですか。また、化学プラントにおいて火災発生時のドミノ効果を防止するためにどのような対策を行っていますか。
A17
ドミノ効果とは1つの事故が引き金となり次々に事故が拡大していく、いわゆる将棋倒しのことです。
化学プラントで火災が発生したならば初期消火と隣接設備への延焼を防止することがドミノ効果防止にあたっての基本です。
消火設備としては、泡消火設備、粉末消火設備、水噴霧消火設備などがあります。
防火設備は、装置に散水して冷却する冷却散水設備、放水設備のほか火災からの放射熱を低減するための水幕設備などがあります。
これらを総称して防消火設備と称しており、それぞれの設備を適切に組み合わせることが必要です。
なお、ドミノ効果防止にあたっては、消火活動用の空地や消防車両通行用の道路などのレイアウトにも配慮を払う必要があります。

Q18
ヒューマンファクターとヒューマンエラーは、どう違うのですか。
A18
ヒューマンエラーとは、人間の行動が、システムの設計上の想定や期待から逸脱してしまった場合の行動を言います。 その原因はさまざまなものがあり、必ずしも人間側の問題ではないことも少なくありません。
しかし、この「エラー」という表現は、ともすれば「間違っている」「悪い」ものという意味にとらえられ、問題が人間側にあるような印象を与えてしまいます。
このため最近では、あえてヒューマンエラーという言葉を用いず、人間的要因という意味のヒューマンファクターという用語が使われるようになっています。

Q19
スリップとミステイクの違いがよくわかりませんが、どのように違うのですか。
A19
ラプスが「行動し忘れている」という行動欠落のエラーであるのに対し、スリップとミステイクは、いずれも行動してはいるもののそれが間違っているというもので、一見すると似ています。
両者の違いは、人間の情報処理のどの段階で間違ったかということにあります。
スリップは、状況を判断し対応行動を意思決定するまでは正しい認識を持ちながら、実際の行動段階で自分の意図と異なった行動をとってしまうというものです。
いわば「手が滑った」のがスリップです。
一方、ミステイクは、そもそもの状況認識や意思決定が間違っているというものです。
行為そのものは本人の意図どおりでも、意図そのものが間違っている場合で、例えば「思い違い」などはこれに当たります。

Q20
ヒューマンファクターのモデルとしては、m-SHELモデルのほかに何がありますか。
A20
例えば、Man(人間)、Machine(機械・設備)、Media(作業環境)、Management(管理)の4つの要因に区分する4Mという考え方があります。
もともとm-SHELモデルも、航空分野で提唱されたSHELモデルを原子力分野において改良したもので、医学界ではこれに加えてP(Patient:患者)を入れたP-mSHELモデルを利用する場合もあります。
ヒューマンファクターのモデルは、あくまでも様々な側面から考えるためのモデルで、正解というものはありません。 それぞれの分野・立場に応じて、工夫しながら考えていくことが大切です。

Q21
ヒューマンエラーが発生して困っています。何か抜本的な対策はありませんか。
A21
残念ながら、ヒューマンエラー対策として「これをやれば大丈夫」というものはありません。
様々な対策を組み合わせて、その発生する可能性をできるだけ小さくしていくことが必要です。
そのための考え方として、例えば図のようなものも提案されています。
図の中で、左側に提示されている考え方ほど、根本対策となります。
最も根本的な対策は、そのエラーをしてしまう作業そのものをなくすことですが、それは容易ではないでしょう。
その場合は、間違った行動を「できないようにする」、正しい行動を「やりやすくする」などの対策が考えられます。 いずれにしても、まずは作業者本人ではなく、周辺環境を整えることに重点が置かれていることに留意しましょう。
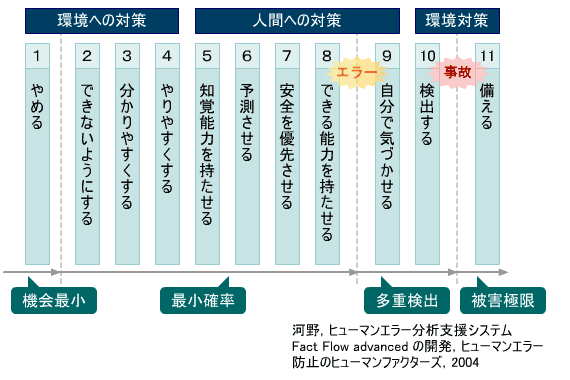

Q22
チームエラーを防止するための訓練方法とは何ですか。
A22
チームのための訓練方法としてよく知られているものには、航空界で開発されたCRM(クルー・リソース・マネジメント,Crew Resource Management)訓練があります。
この訓練方法は、関係する人々の持つ能力や情報を「人的資源(リソース)」としてとらえ、それを十分に活用して最も良い意志決定をするために、コミュニケーションやメンバー間の連携について訓練するというものです。
当初は、パイロットを対象としていたので「コックピット・リソース・マネジメント」と称していましたが、近年ではコックピット内だけでなく他の人々をも人的資源として考え、このように名称が変更になりました。
同様の訓練方法は、航空機の整備や客室乗務員の現場でも取り入れられています。
また最近では、医学界でも類似の手法が導入され、チーム医療の確立による医療事故防止が目指されています。

Q23
化学プラントは大量の危険物質を取り扱っているのでリスクは高いと考えるのでしょうか。また、リスクを小さくするには何が必要ですか。
A23
化学プラントのリスクは、事故の起こり易さ(発生確率)と事故が発生した際の影響の大きさを組み合わせて算定します。
化学プラントの多くは可燃性物質、毒性物質などの危険物質を大量に取り扱っており潜在的な危険性はあるといえます。
しかし、化学プラントは事故の発生防止ならびに事故が発生した際の影響の大きさを抑制するために安全防災設備を設置して安全を確保しリスクを小さくしているといってよいでしょう。
なお、リスクを低く抑えるためには、事故の発生確率を低く抑えることを第一に考えるべきですが、万一事故が発生した場合を想定し、被害の局限化の対策を講じておくことが必要です。
このため、安全設備の健全性を確保するため定期的な点検や保守保全などの管理が重要といえます。

Q24
危険源の特定にあたって、複数のメンバーからなるチームで検討を行うのは何故ですか。
A24
化学プラントは多様な工程から成り立っている大規模なマン・マシンシステムなので1人で危険源の特定を行うには限界があります。
このため、プロセス特性を理解している技術者、制御システム技術者、運転特性を理解しているオペレータなど専門分野の異なるメンバーからなるチームを編成して検討を行うことが重要です。
三人よれば文殊の知恵というわけではありませんが、メンバーそれぞれが自分の専門領域から検討を行うことにより、多角的で、かつ、見落としの少ない検討ができます。

Q25
What-if、HAZOP、故障モード影響解析、フォールトツリー解析、イベントツリー解析はいつ頃から使用されたのですか。
A25
What-if解析については良く分かりません。
HAZOPは1960年代の初めにイギリスのICI(Imperial Chemical Industry)という化学会社が自社の有機化学プロセスの安全性評価のために開発した手法です。
故障モード影響解析は、1950年代半ばに航空機エンジンの信頼性解析に使用されていたといわれています。
フォールトツリー解析は、1960年代初めに、米国のベル研究所がミニットマンロケットの信頼性解析に使用したのが始まりといわれています。
イベントツリー解析の起源は分かりませんが、米国で実施された原子力プラントのリスクアセスメントにフォールトツリー解析とともに使用されています。
このリスクアセスメントの報告書が1975年に出ているので、1970年代前半から使用されていると考えられます。

Q26
リスク解析にあたり、What-if解析、HAZOP、故障モード影響解析、フォールトツリー解析、イベントツリー解析はどのような使い分けとなるのでしょうか。
A26
化学プラントのリスク解析は、プラントに内在する潜在的な危険源を特定し、危険源が事故として現われる確率と事故発生時の影響の大きさを組み合わせてリスクの大きさを算定します。
What-if解析、HAZOP、故障モード影響解析は、化学プラントの構成機器の故障や人間の操作ミスが発生したことを想定し、それがどのような危険事象につながるかどうかを検討する危険源特定手法です。
一方、フォールトツリー解析は、反応暴走などの事故がどのような原因の組み合わせで発生するのかを解析したのちに、反応暴走などの事故の発生確率を推算する手法です。
イベントツリー解析は、装置から危険物質が漏洩したときに、漏洩検知器や緊急遮断システムなど安全設備の成功・失敗に応じてどのような災害事象に進展していくのかを解析したのちに、それぞれの災害事象の発生確率を推算する手法です。

Q27
フォールトツリー解析においてブール代数を使ってツリーを整理していきますが、ブール代数において、A+A=A、A・A=Aという関係式がありますが、これはどういう意味ですか。又、何故そのようになるのかを分かりやすく説明してください。
A27
フォールトツリー解析は、起こって望ましくない事象がどのような原因の組み合わせで発生するのかをANDゲートとORゲートを使ってツリーを作成して解析していきます。
AとBという事象が同時に発生したときにTという事象が発生する場合はANDゲートが使われ、論理演算式では「T=A・B」という式になります。
これは「AかつBが成り立ったときにTが成り立つ」ということを意味しています。
また、AもしくはBが発生したときにTという事象が発生する場合はORゲートが使われ、「T=A+B」という式になります。
これは「AもしくはBが成り立ったときにTが成り立つ」という意味になります。
質問の「A・A=A」は「AかつAが発生した。すなわちAが発生した」、「A+A=A」は、「AもしくはAが発生した。
すなわちAが発生した」ということを意味しています。

 |